SCI论文(www.lunwensci.com)
摘要:3D 打印技术是一种快速成型技术, 具有成本低、快速高效、更大的设计自由等优势。 3D 打印技术应用在催化剂领域可以降 低传统催化剂制备方法的复杂程度, 有利于调控催化剂材料的结构和成分, 最大限度提高材料的催化性能。为优化和促进催化剂 材料的发展带来了广阔的前景。首先简单介绍了 3D 打印技术的概念以及在催化研究中最常用的几种应用方法, 然后着重概述了近 5 年来几种常见的工艺打印催化剂材料的最新研究成果, 最后对其发展趋势进行了展望。为深入开展 3D 打印催化剂材料研究和应 用提供了一定的参考作用。
Application Status and Prospect of 3D Printing Technology in the Field of Catalyst Preparation
Liu Zhongwen1. Geng Fengfei2※, Chen Shenggui3. Xu Jianhui1※
( 1. School of Environment and Civil Engineering, Dongguan University of Technology, Dongguan, Guangdong 523808. China; 2. Shenyang
Chemical Industry School, Shenyang 110122. China; 3. School of Art Design, Guangzhou Panyu Polytechnic, Guangzhou 511483. China)
Abstract: 3D printing technology is an additive manufacturing technology and has the advantages of low cost, fast and efficient, and greater
freedom of design. 3D printing technology applied in the field of catalysts can reduce the complexity of traditional catalyst preparation methods,
and facilitate the regulation of the structure and composition of catalyst materials, maximize the catalytic performance of the materials.
Therefore it holds prominent prospect for optimising and promoting the development of catalyst materials . The concept of 3D printing
technology and several of the most commonly used printing methods currently applied in catalytic research were introduced, then the latest
research results of several common processes for printing catalyst materials over the last five years were highlighted, and finally an outlook on
their development trends was provided. The paper provides a certain reference role for in-depth research and application of 3D printed catalyst materials.
Key words: 3D printing technology; additive manufacturing; catalyst
0 引言
2015 年 5 月 8 日, 国务院发布 《中国制造 2025》, 明 确表明了 3D 打印技术作为一门新兴技术占有的重要性, 并且体现出我国对 3D 打印技术产业发展的重视[1]。近年 来, 3D 打印技术作为一种新颖的加工工艺, 除了在教 学[2]、医疗[3]、航空航天[4] 以及工程建筑[5] 等领域中有所 应用外, 在催化领域中也掀起了一股热潮, 大量相关成 果不断涌现[6-8]。
随着 3D 打印技术和催化剂应用的迅速发展, 为了满 足催化剂制备成本低、制备技术简单以及催化效率高、 效果卓越等要求, 近年来国内外研究人员已经利用不同 的 3D 打印工艺制备出满足条件的催化剂并成功应用到催 化领域当中。此外, 由于 3D 打印的方法可以更好地控制 目标材料的精细结构, 其安装和运营成本也随着 3D 打印技术的发展迅速下降[9]。因此, 3D 打印技术在催化剂领 域中的重要地位越来越突出, 推动了催化领域的发展。
本文在简要介绍 3D 打印技术的发展现状及其基本原 理的基础上, 对近 5 年来 3D 打印技术在催化剂领域的研 究成果进行了详细的归纳。从不同类别的 3D 打印工艺在 催化剂系统应用当中进行了分析, 主要着重分析了不同 工艺在不同的催化剂系统当中的优势与不足。最后, 提 出了 3D 打印技术在催化剂领域中的发展趋势和面临的挑 战。为深入开展 3D 打印催化剂材料研究和应用提供了一 定的参考作用。
1 3D 打印技术简介
3D 打印技术又被称为增材制造 (AM) 技术[10- 12], 与传统的减材技术不同, 作为一门新兴的技术, 3D 打印 是一门结合数字模型文件, 采用不同的原材料通过逐层打印而获取目标产物的快速成型技术[13]。根据不同的工 作原理, 3D 打印技术可以分成不同的种类。根据 O.H. Laguna 等统计的数据[14] (图 1), 目前应用在催化研究中 最常用的打印方法分别是直写成型 (DIW)、熔融沉积成 型 (FDM)、 立 体 光 刻 成 型 (SLA)、 选 择 性 激 光 熔 融 ( SLM) 和选择性激光烧结 (SLS) 等。
3D 打印技术最早起源于美国, 1984 年, Charles Hull 发明了 SLA 3D 打印技术并获得了专利。随后, 他创立了 3D Systems 公司后研发出了第一台光固化 3D 打印机。随 后, SLS 、FDM 、LOM 、3DP 等 3D 打印技术相继被开发。 至今, 3D 打印技术已经研发出了多种不同成型原理的工 艺, 应用到了不同的领域当中。 3D 打印技术具有速度快 以及设计自由度高等优势。尽管我国引入 3D 打印技术的 时间较短, 随着对 3D 打印技术的探索和突破, 该技术对 我国科技和文化方面的发展起到了一定的作用。例如, 成都市驿马河公园的“流云桥” [15]就是我国利用 3D 打印 技术研发制造出来的。
2 3D 打印技术在催化领域中的应用
2.1 直写成型 (DIW)
DIW 是一种用于 3D 打印的基于挤出成型的技术[16]。 以剪切稀化流体浆料为打印原料, 能够在挤压过程中保 持形状, 而且 3D 物体形成时不会发生坍塌。 DIW 技术在 陶瓷和石墨烯基等制造上已经取得了非常大的进展[17- 18]。 在所有的 AM 技术研究中, DIW 可以在复杂的几何形状 中比较容易和快速地制造陶瓷基材料。通过 DIW 技术可 以制备结构极其复杂的陶瓷部件, 利用这些具有复杂结 构的陶瓷作为催化剂的载体, 可以增加活性组分的负载 率, 进而提高催化效果。
Liu[19]等使用 DIW 工艺设备, 利用气相 SiO2 基触变油 墨制造了不同的 3D 结构, 墨水在空气中逐层印刷在特氟 龙板基材上, 再经过挤压压力和干燥等步骤之后形成了 分层多孔陶瓷。通过水热处理的方法, 使用前驱体溶液 将 MOFs (金属有机框架) 原位生长到陶瓷结构上, 最 后获得了 3DP-HPC@MOFs 负载催化剂。所获得的 3D 打 印分级多孔陶瓷载体增加了 MOFs 的负载, 提供了更多 的活性位点, 加速反应物的运输, 从而提高了污染物的 催化降解性能。 Liu 等将 MB 、Rh B 、MG 和 CV4 种不同 的染料混合在一起以模拟现实中的有机污染物。在 3DPHPC@MOFs 负载催化剂的催化下, 混合水溶液染料逐渐 降解, 并在 20 min 内显示无色溶液并且催化降解后没有 发生任何的变形和坍塌, 具有较高的降解效率和长期稳 定性。
Huo[20] 等结合 DIW 和后处理工艺, 提出了一种制备 具有仿生脉、比表面积和强度皆卓越的多级多孔氧化铝 陶瓷的新方法。以拟薄水铝石作为前驱体、粘合剂和成 孔剂获得胶体墨水, 经过剪切减薄的方法使胶体墨水容 易在压力下挤压, 并在打印后固化以进行 3D 形状控制。 DIW 工艺过程使用的是三轴 3D 打印机, 然后将样品冷冻 干燥后进行第一次烧结后处理。样品在胶体二氧化硅中 浸泡 30 min 后再进行第二次烧结后处理。传统的多孔陶 瓷催化剂成型工艺对于高度复杂的几何形状和相互连接 的孔隙结构的成型比较困难, 然而, Huo 等结合 DIW 工艺解决了这些难题。负 载 Ni/P 的仿生陶瓷作为 NiPB 催化剂在甲烷干重 整反应 (DRM) 测试中 表 现 出 良 好 的 催 化 效 果。在 800 ℃的条件下, CH4 和 CO2 在 该 催 化 剂 上的平均转化率分别是 36.2% 和 42.8%。相比之 下, 基于 3D 打印仿生氧 化铝陶瓷制备的 NiPB 催 化剂的 DRM 性能处于中 等水平。
2.2 熔融沉积成型 (FDM)
FDM 也是 3D 打印技术应用在催化领域中的一种重 要的技术之一。与 DIW 相似, FDM 也是属于挤出成型的 类型。在 FDM工艺中, 热塑性聚合物被加热到略高过熔 点的温度后, 通过移动的加热喷嘴挤压并逐层沉积在平 台上[21-22] 。FDM 的一个缺点是复合材料必须呈长丝形式 才能实现挤出工艺, 另外它可用材料仅限于具有合适熔 体粘度的热塑性聚合物。尽管如此, FDM 打印机也具有 较低的成本、高速、简单性且允许同时沉积不同的材料 等的优点[23]。目前, 很多研究利用 FDM 工艺制备出催化 载体后, 再引入其他的活性组分提高催化材料的催化性 能。另一种方式是在催化载体表面负载活性组分[13]。
Sangiorgi A[24]等从可再生生物资源中获取了生物聚合 物聚乳酸 (PLA) [24], 采用 FDM 制备了氧化态基光催化 过滤器。 FDM 使用传统的 3D 打印机将挤出的细丝进行 了制造支架。并通过甲基橙 (MO) 在水溶液中的降解性 能来对光催化的活性进行了评价。通过控制打印机参数, 3D 支架的几何形状发生了变化, 导致 70 ∶ 30 (wt/wt)PLA: PEI-TiO2 复 合 材 料 中 实 现 了 MO 的 降 解 率 达 到 了 100%。此外, FDM 还被广泛应用在电催化电极材料的研 究中, FDM 是制造热塑性电极 (包括 PLA 、ABS 和聚氨 酯) 的 首 选 3D 打 印 技 术[26] 。 Raquel G Rocha[27] 等 通 过 FDM 生产了 3D打印热塑性电极, 证明了 3D 打印参数是 可以明显影响 3D 打印 CB/PLA 电极的电化学性能。且发 现较低的打印周长速度 (30 mm/s) 可以降低电极的电荷 转移电阻。
Mackiewicz E[28] 的团队以镍颗粒用作填料, 将聚合 物 -金属 (PLA Ni 5% 、PVB Ni 25% 和 ABS Ni 25%) 复 合材料以细丝的形式挤出, 然后用于 3D FDM 打印 (图 3、图 4)。他们对 3D打印的复合材料进行热处理以去除 聚合物并烧结镍颗粒, 还使用泡沫镍作为基材制备了 3D 印刷复合材料。结果表明, 经过热处理后形成了开口孔 隙率高于 60% 的金属结构, 同时增加催化剂的最终孔 隙率和机械强度。这使得该催化剂适合于进一步的催化 测试。
Hock S[29] 等通过聚苯乙烯细丝的 FDM 设计并印刷了 具有复杂传输孔通道的定制整体。随后, 通过磺化引入 磺酸基团, 以催化官能化结构化单体的可接近内表面。 并选择蔗糖的水相水解作为催化试验反应。结果证明该 催化剂表现出了更好的催化性能, 这是由于孔通道表面 上可接近的官能团更好, 因此避免了大孔离子交换树脂作为催化剂的严重传质限制。
2.3 立体光刻成型 (SLA)
SLA 具有分辨率高、速度快等的特点, 是目前应用 在催化领域中最热门的 3D 打印技术之一。 SLA 基本原理 是光聚合[30], 是液体光聚合物树脂在暴露于紫外光辐射 时会转化为固体聚合物[31], 不断重复这个过程可以制造每个分层组分[32]。由于打印部件可以归类为各向同性且 打印的物体具有出色的表面光洁度和非常低的阶梯效应, SLA 对比于其他的 AM 技术 (比如 FDM) 具有巨大的优 势[33]。但是, SLA 中使用的树脂成本非常高, 是一个显 著缺点。
Mei H[34] 等采用 SLA 3D 打印技术制备了 3 种具有规 则通孔的片状载体样品 (图 5), 并且进一步在 N2 的环境 下进行烧结得到了碳陶瓷载体。然后将选择作为典型催 化剂的二硫化钼 (MoS2 ) 通过水热法分别负载在烧结碳 陶瓷载体和陶瓷载体上, 讨论了载体-催化剂体系的稳 定性和光吸收效率。结果表明, 碳载体对 Rh B 染料分子 的降解效率明显提高了 28% 以上, 对于相同的几何阵列 图 案, 碳 载 体 的 光 降 解 效 率 从 51.86% 显 著 提 高 到 64.83%, 而陶瓷载体的光降解效率仅提高到 57.78%。该 催化剂载体体系具有优异的稳定性, 在 2 次循环后降解 效率下降到 87.65%, 而在 5 次循环后的稳定在 82.35% 左 右, 效率下降可能是由于搅拌时催化剂的质量损失。
Franchi F S[35] 等使用 SLA 3D打印机和耐热树脂制造 出了比金属打印结构价格更低、精度更高的样品。通过 旋涂沉积 3%Pd/CeO2 涂层, 然后用 N2/H2 进行两步原位煅 烧/还原, 将这些树脂载体催化活化, 以实现富 H2 氧化。
2.4 选择性激光熔融 (SLM) 和选择性激光烧结 (SLS)
SLM 和 SLS 都是属于粉末成型的方法, 二者原理类 似, 区别主要在于 SLS 一般是用高分子材料作为粘合剂, 而 SLM是不需要粘合剂和低熔点部分。 SLM 是一种特殊 的快速成型技术, 旨在使用高功率密度激光通过在层内 与层之间选择性地熔化和熔化金属粉末来构建组件[36]。 SLS 的过程包括粉末沉积, 粉末凝固, 然后将构建平台 降低一层厚度。重复这 3 个步骤, 直到制造零件的最后 一层烧结完毕[37]。粉末材料可以是金属合金材料[38-40]、 聚合物[41] 和陶瓷。与其他 3D 打印技术相比, SLM 在应用 中更加灵活, 尤其是在制备金属催化剂材料领域, 是目 前发展最快的 3D 打印技术之一。
以 3D 打印的方式将还原剂掺杂于活性催化剂中能够 实现高效且可持续的废水处理[42] 。Yang[43]等将 Cu 作为还 原剂引入到金属玻璃基催化剂中, 并通过 SLM 技术构建 了壁厚 1 mm、通道宽度 1.4 mm 的蜂窝状 MG/Cu 催化剂。 该催化剂可以循环 100 次以上而催化活性没有发生明显 的下降, 表现出了极高的可重复利用性。对于废水中典 型的有机污染物 Rh B 染料, 3D 打印的蜂窝状 MG/Cu 催 化剂可以在 5 min 内完全将其脱除, 相比于商用 ZVI 催化 剂 (11 min 只降解 70%) 快得多。
Yan[44] 等利用 SLM 技术结合脱合金工艺设计了三维 分层多孔 CuAg 双金属催化剂, 并进行了 CO2 的电还原研 究。与此前报道的 CuAg 纳米催化剂产生各种多碳产物不 同, Yan 等人设计的分层多孔 CuAg 显示出了较高的 CO2 电催化合成气 (CO+H2 ), 在-0.8~- 1.0 V ( vs RHE) 范围 内表现出 92% 以上的法拉第电流效率。此外, 他们进一 步利用 SLM 技术制备了 CuAg 蜂窝电极, 该结构表现出 优异的电化学稳定性, 连续工作约 140 h 没有发生明显的 衰减。根据 Yan 等研究发现, 这是迄今为止报道的最高 值。该工作为结合 3D 打印技术开发稳定的合成气电催化 剂提供了一种新的思路。
Elmeri Lahtinen[45] 等利用 SLS 工艺制备了多相加氢催 化剂, 在苯乙烯、环己烯和苯乙炔的氢化反应中测试了 含有 10% (wt)Pd/SiO2 的 3D 打印搅拌棒的催化性能。结 果表明, 环己烯作为底物时, 非打印粉状催化剂转化率 为 69.2%, 表现得比转化率为 36.4% 的 3D 打印催化剂好 得多, 这是由于其空间受阻的双键的影响。而在苯乙烯 和苯乙炔的情况下, 3D 打印对其总活性的影响很小。此 外, 他们制备的催化剂还具有高的热性能和力学性能。 2.5 其他工艺在催化领域中, 由于单原子位点催化剂 ( SASCs ) 可以最大限度地利用原子和分离活性位点, 表现出优异 的性能, 近年来成为了催化研究中的热点[46]。然而, 一 些 SASCs 存在着低金属负载的问题, 导致催化剂失活速度迅速、目标产物产率低等。为了提高单原子催化剂 ( SACs) 的催化性能, Zhang[47] 等开发了一种 3D 打印方 法, 可以制造出所需几何形状的 SACs。图 6 (a) 是该方 法的过程示意图。 Zhang 等人获取了低成本的用作油墨 的天然聚合物、明胶和甲基丙烯酰化明胶 (GelMA) 作 为 3D 打印的原材料。前驱体通过 3D 打印直接自动构建, 如图 6 (b) 所示, 随后冷冻干燥去除残留的水分。接 着, 冷冻干燥的样品被热裂解, 得到可以在明胶或 Gel⁃ MA88 衍生碳上的 3D 打印 SACs 。通过这种方法得到的 SACs 的结构在热解后能够很好地保持, 如图 6 (c) 所 示。 Zhang 等表明, 通过改变印刷油墨中的相应金属 ( Co 和 Ni) 乙酰丙酮前驱体的浓度, 可以提高分离反应 中心的金属负载量, 从 3.9% 增大为 20.8%。该方法为碳 基 SACs 的研究提供了有价值的参考, 然而该技术不适用 于具有各种载体的 SACs 的合成, 比如半导体和沸石。
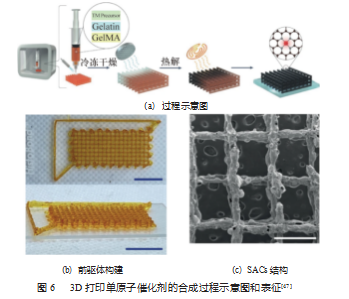
Agueniou F[48] 等首次提出了金属整体的 3D 打印, 复 制了正真的蜂窝设计及其在多相催化过程中的应用。通 过直接激光烧结 (DMLS) 从不锈钢粉末中 3D 打印获得 了金属蜂窝整体作为载体, 并通过水洗法制备了负载在 CeO2-ZrO2 上的镍蜂窝整体催化剂。 DRM 结果表明: 3D 打印的整体结构不仅显示出作为镍催化剂载体的性能, 而且其本身也具有内在活性, 反应物转化率在 900 ℃时 接近 50%。
氧化铝基催化剂占工业负载催化剂的约 70%, 但直 接使用数字光处理 (DLP) 方法很难制备 γ-Al2 O3 结构的 催化剂载体。 Wang 等[49] 提出采用 DLP 技术直接制备 γ - Al2 O3 结构催化剂载体的光固化树脂配方 (图 7), 并分析 了其成型和烧结过程的特点。使用 DLP 形成的 γ -Al2 O3 可以精确控制其孔隙率和结构, 从而减轻反应区的压降, 提高传质效率。
3 展望
通过上述总结可以看出, 3D 打印技术用于催化剂领 域, 不同的工艺都可以起到一定的作用。与传统的方法 相比, 3D 打印技术为催化领域制造了新的可能, 尤其是 在更准确地调整功能材料的结构以及改变材料的化学成 分方面[50] 。3D 打印技术可以制造具有高表面积的复杂结 构, 从而提高催化反应的速率。催化功能可以通过 3 种 不同的方法实现: 通过在印刷过程之前或之后修改印刷 材料的化学成分, 或者通过从具有固有催化特性的材料 中打印零件[51]。
3D 打印技术是制造多孔材料的最有利技术之一。然 而, 尽管利用 3D 打印工艺制备催化剂有优势, 该领域还 是存在一些需要解决的挑战性问题, 获得更理想的催化 剂材料仍需努力。
( 1 ) 3D 打印的原材料有待进一步开发。尤其是致力 于开发既能满足高效、高精度且经济的要求, 又能具备 卓越催化能力和高机械强度等功能要求的催化剂。当前 材料仍然是限制 3D 打印技术应用的关键因素。此外, 多 材料打印的局限性仍然比较大, 目前 3D 打印工艺制备高 性能催化剂多数是单一材料打印。因此, 需要加强多材 料在 3D 打印工艺制备催化剂领域的应用型研究。
( 2) 催化剂需要进行优化。 3D 打印技术可以调整催 化剂材料的分层孔隙率、孔特征以及活性位点的分布情 况, 从而进一步实现催化剂的高负载率。因此对催化剂 进行优化显得尤为重要。此外, 3D 打印不同形状的催化 剂样品之间存在不同的催化效率, 其中的具体影响过程 还待进一步深究。
( 3) 致力于发展新型 3D 打印工艺用于催化剂制备领 域上, 尤其是发展一些具有新颖成型机理的 3D 打印技 术。随着科技的发展, 新颖的 3D 打印工艺越来越受到人 们的关注, 并出现了一些带有突破性的研究成果。如, 结合 DLP 和 SLA 技术, 实现高效率、高精度的 3D打印; iCLIP[52] 新技术的开发: 除了速度上的优势, iCLIP 还可 以多种树脂同时打印。因此, 积极研发新型的 3D 打印工 艺有利于进一步提高催化剂制备的效率。
( 4) 目前, 3D 打印技术在催化剂制备领域中有了一 定的研究成果。然而,多数的研究成果投入实际工业应用中比较困难,一般存在生产效率低或者生产成本高等一系 列问题。如何实现规模化的放大, 将 3D 打印技术投入工 业中制备高性能的催化剂是接下来值得探究的问题。
随着中国制造 2025 计划的不断发展, 3D 打印工艺 在各方面都得到一定的优化。作为一种新兴的工艺技术, 为催化剂材料的发展提供了机会。在 3D 打印技术制备催 化剂材料等方面不断取得了重要的成果, 相信这将为 3D 打印技术促进催化剂材料的发展带来新的可能。随着 3D 打印技术理论的完善和仪器设备的开发, 不断取得的重 大突破, 势必将 3D 打印工艺在催化剂领域的应用推到另 一个新的高度。
4 结束语
目前通过 3D 打印技术制备催化剂材料, 提高催化效 果是非常有前景的一种方式。本文对近 5 年 3D 打印技术 的几种常见工艺在制备催化剂材料的最新研究成果进行 了详细的归纳, 包括 DIW 、FDM 、SLA 、SLM 、SLS 等工 艺。同时, 对不同的工艺原理进行了简单的介绍。总的 来说, 制备催化剂材料的 3D 打印工艺有各自的优势和不 足。不同的工艺对于制备催化剂材料有不同的要求, 尤 其是对于打印原材料的要求。这一领域的快速发展解决 了传统方法制备催化剂材料中成本高、效率低及高度复 杂几何形状制备困难等挑战性问题。本文为深入开展 3D 打印催化剂材料研究和应用提供了一定的参考作用, 对后续其他利用 3D 打印催化剂材料的工作提供了新的 思考。
参考文献:
[1] 于灏 . " 中国制造 2025"下的 3D 打印[J]. 新材料产业 , 2015. 260(7): 20-27.
[2] 何桂明, 张铭, 张勇富 . 利用 3D 技术打印的平面镜视错觉作品 [J]. 广西物理,2021.42(2):31-33.
[3] 刘宸希, 康红军, 吴金珠, 等 . 3D 打印技术及其在医疗领域的 应用[J]. 材料工程, 2021. 49(6): 66-76. [4] 吴强收 . 3D 打印技术在航空航天领域中的应用[C]//第五届空 天动力联合会议暨中国航天第三专业信息网第 41 届技术交 流会, 南京:中国科协,2020: 38-42.
[5] 冯鹏, 张汉青, 孟鑫淼, 等 . 3D 打印技术在工程建设中的应用 及前景[J]. 工业建筑, 2019. 49(12): 154- 165.
[6] LAWSON S, LI X, THAKKAR H, et al. Recent advances in 3D printing of structured materials for adsorption and catalysis appli ⁃ cations[J]. Chemical Reviews, 2021. 121(10): 6246-6291.
[7] MCQUEEN A D, BALLENTINE M L, MAY L R, et al. Photocata⁃ lytic degradation of polycyclic aromatic hydrocarbons in water by 3D printed TiO2 composites[J]. ACS ES&T Water, 2022. 2(1): 137- 147.
[8] LAWSON S, ALWAKWAK A-A, ROWNAGHI A A, et al. Gel- Print-grow: a new way of 3D printing metal-organic frameworks[J]. ACS applied materials & interfaces, 2020. 12(50): 56108- 56117. [9] ZHOU X, LIU C J. Three-dimensional Printing for catalytic ap ⁃ plications: current status and perspectives[J]. Advanced Func ⁃ tional Materials, 2017. 27(30): 1701134.
[10] CALIGNANO F, MANFREDI D, AMBROSIO E P, et al. Over⁃ view on additive manufacturing technologies[J]. Proceedings of the IEEE, 2017. 105: 593-612.
[11] SINGH S, RAMAKRISHNA S, SINGH R. Material issues in ad⁃ ditive manufacturing: a review[J]. Journal of Manufacturing Pro⁃ cesses, 2017. 25: 185-200.
[12] KRUTH J P. Material increase manufacturing by rapid prototyp ⁃ ing techniques[J]. CIRP Annals, 1991. 40(2): 603-614.
[13] 周昕瞳, 刘振星, 刘昌俊 . 3D 打印在催化和吸附材料制备领 域的应用[J]. 化工进展, 2019. 38(1): 516-528.
[14] LAGUNA O H, LIETOR P F, GODINO F J I, et al. A review on additive manufacturing and materials for catalytic applications: milestones, key concepts, advances and perspectives[J]. Materi⁃ als & Design, 2021. 208: 109927.
[15] 陆承麟, 陈晓明, 龚明, 等 . 超大尺度 3D 打印景观桥制造技 术研究[J]. 施工技术(中英文), 2021. 50(21): 68-71.
[16] LEWIS J A. Direct ink writing of 3D functional materials[J]. Ad⁃ vanced Functional Materials, 2006. 16(17): 2193-2204.
[17] SHAHZAD A, LAZOGLU I. Direct ink writing (DIW) of struc ⁃ tural and functional ceramics: Recent achievements and future challenges[J]. Composites Part B: Engineering, 2021. 225: 109249. [18] PINARGOTE N W S, SMIRNOV A, PERETYAGIN N, et al. Di⁃ rect ink writing technology (3D printing) of graphene-based ce ⁃ ramic nanocomposites: a review[J]. Nanomaterials, 2020. 10(7). [19] LIU D, JIANG P, LI X, et al. 3D printing of metal-organic frameworks decorated hierarchical porous ceramics for high-ef⁃ ficiency catalytic degradation[J]. Chemical Engineering Journal, 2020. 397: 125392.
[20] HUO C, TIAN X, CHEN C, et al. Hierarchically porous alumina catalyst carrier with biomimetic vein structure prepared by di ⁃ rect ink writing[J]. Journal of the European Ceramic Society, 2021. 41(7): 4231-4241.
[21] VANĚČKOVÁ E, BOUŠA M, NOVÁKOVÁ LACHMANOVÁ Š, et al. 3D printed polylactic acid/carbon black electrodes with nearly ideal electrochemical behaviour[J]. Journal of Electroana⁃ lytical Chemistry, 2020. 857: 113745.
[22] SZTORCH B, BRZĄKALSKI D, PAKUŁA D, et al. Natural and synthetic polymer fillers for applications in 3D printing-FDM technology area[J]. Solids, 2022. 3(3): 508-548.
[23] WANG X, JIANG M, ZHOU Z, et al. 3D printing of polymer ma⁃ trix composites: A review and prospective[J]. Composites Part B: Engineering, 2017. 110: 442-458.
[24] SANGIORGI A, GONZALEZ Z, FERRÁNDEZ-MONTERO A, et al. 3D printing of photocatalytic filters using a biopolymer to immobilize TiO2 nanoparticles[J]. Journal of The Electrochemi ⁃cal Society, 2019. 166(5): H3239-H3248.
[25] ILYAS R A, SAPUAN S M, HARUSSANI M M, et al. Polylactic acid (PLA) biocomposite: processing, additive manufacturing and advanced applications[J]. Polymers, 2021. 13(8).
[26] BROWNE M P, REDONDO E, PUMERA M. 3D printing for electrochemical energy applications[J]. Chemical reviews, 2020. 120(5): 2783-2810.
[27] ROCHA R G, RAMOS D L O, DE FARIA L V, et al. Printing parameters affect the electrochemical performance of 3D-print⁃ ed carbon electrodes obtained by fused deposition modeling[J]. Journal of Electroanalytical Chemistry, 2022. 925: 116910.
[28] MACKIEWICZ E, WEJRZANOWSKI T, ADAMCZYK- CIESLAK B, et al. Polymer-nickel composite filaments for 3D printing of open porous materials[J]. Materials (Basel), 2022. 15 (4):1360.
[29] HOCK S J, REIN C, ROSE M. 3D-Printed Acidic Monolithic Catalysts for Liquid-Phase Catalysis with Enhanced Mass Transfer Properties[J]. ChemCatChem, 2022. 14(8).
[30] PAGAC M, HAJNYS J, Ma Q-P, et al. A review of vat photopo⁃ lymerization technology: materials, applications, challenges, and future trends of 3D printing[J]. Polymers, 2021. 13(4): 598. [31] BÁRTOLO P J S. Stereolithography: Materials, Processes and Applications[M]. US:Springer Basel AG,2011.
[32] MARTÍNEZ-PELLITERO S, CASTRO M A, FERNÁNDEZ- ABIA A I, et al. Analysis of influence factors on part quality in micro-SLA technology[J]. Procedia Manufacturing, 2017. 13: 856-863. [33] ARAVIND SHANMUGASUNDARAM S, RAZMI J, MIAN M J, et al. Mechanical anisotropy and surface roughness in additively manufactured parts fabricated by stereolithography (SLA) using statistical analysis[J]. Materials (Basel), 2020. 13(11).
[34] MEI H, HUANG W, LIU H, et al. 3D printed carbon-ceramic structures for enhancing photocatalytic properties[J]. Ceramics International, 2019. 45(12): 15223- 15229
[35] FRANCHI F S, AMBROSETTI M, BALZAROTTI R, et al. Rich H2 catalytic oxidation as a novel methodology for the evaluation of mass transport properties of 3D printed catalyst supports[J]. Catalysis Today, 2022. 383: 123- 132.
[36] YAP C Y, CHUA C, DONG Z, et al. Review of selective laser melting: materials and applications[J]. Applied Physics Re⁃ views, 2015. 2: 041101.
[37] LIGON S C, LISKA R, STAMPFL J, et al. Polymers for 3D Printing and customized additive manufacturing[J]. Chemical Reviews, 2017. 117(15): 10212- 10290.
[38] KLADOVASILAKIS N, CHARALAMPOUS P, TSONGAS K, et al. Influence of selective laser melting additive manufacturing parameters in inconel 718 superalloy[J]. Materials, 2022.
[39] 张赛博,赵俊淞,李小海等 . 金属 3D 打印技术的应用与发展前 景[J]. 装备制造技术, 2022. 335(11): 207-210.
[40] BARRIOBERO-VILA P, GUSSONE J, STARK A, et al. Peri⁃ tectic titanium alloys for 3D printing[J]. Nature Communica⁃tions, 2018. 9(1): 3426.
[41] ZHICHAO L, WANG Z, GAN X, et al. Selective laser sintering 3D printing: a way to construct 3D electrically conductive segre ⁃ gated network in polymer matrix[J]. Macromolecular Materials and Engineering, 2017. 302: 1700211.
[42] SAIDULU D, SRIVASTAVA A, GUPTA A K. Enhancement of wastewater treatment performance using 3D printed structures: a major focus on material composition, performance, challenges, and sustainable assessment[J]. Journal of Environmental Man⁃ agement, 2022. 306: 114461.
[43] YANG C, ZHANG C, CHEN Z J, et al. Three-dimensional hier⁃ archical porous structures of metallic glass/copper composite catalysts by 3D printing for efficient wastewater treatments[J]. ACS Appl Mater Interfaces, 2021. 13(6): 7227-7237.
[44] YAN W Y, ZHANG C, LIU L. Hierarchically porous CuAg via 3D printing/dealloying for tunable CO2 reduction to syngas[J]. ACS Applied Materials & Interfaces, 2021. 13(38): 45385- 45393. [45] LAHTINEN E, TURUNEN L, HÄNNINEN M M, et al. Fabrica⁃ tion of porous hydrogenation catalysts by a selective laser sinter⁃ ing 3D printing technique[J]. ACS Omega, 2019. 4: 12012 - 12017. [46] LIANG X, FU N, YAO S, et al. The progress and outlook of met⁃ al single-atom-site catalysis[J]. Journal of the American Chemi ⁃ cal Society, 2022. 144(40): 18155- 18174.
[47] ZHANG H, LOU X W D. 3D printing of single-atom catalysts [J]. Nature Synthesis, 2023. 2: 81-82.
[48] AGUENIOU F, VIDAL H, DE DIOS LÓPEZ J, et al. 3D-print⁃ing of metallic honeycomb monoliths as a doorway to a new gen ⁃ eration of catalytic devices: the Ni-based catalysts in methane dry reforming showcase[J]. Catalysis Communications, 2021. 148: 106181.
[49] WANG H, WANG P, WANG Q, et al.[J]. Industrial & Engineer⁃ ing Chemistry Research, 2021. 60(35): 13107- 13114.
[50] PANWISAWAS C, TANG Y T, REED R C. Metal 3D printing as a disruptive technology for superalloys[J]. Nature Communi⁃ cations, 2020. 11(1): 2327.
[51] CAPEL A J, RIMINGTON R P, LEWIS M P, et al. 3D printing for chemical, pharmaceutical and biological applications[J]. Na⁃ ture Reviews Chemistry, 2018. 2(12): 422-436.
[52] GABRIEL L, TIM S, KAIWEN H, et al. Injection continuous liquid interface production of 3D objects[J]. Science Advances, 2022. 8(39): eabq3917.
关注SCI论文创作发表,寻求SCI论文修改润色、SCI论文代发表等服务支撑,请锁定SCI论文网!
文章出自SCI论文网转载请注明出处:https://www.lunwensci.com/ligonglunwen/59351.html