SCI论文(www.lunwensci.com)
摘要 :文章分析 14Cr1MoR 大厚度钢的热处理方法。开展 热处理试验,对试验材料、设备与方案提出严格要求。在具体 试验中,要严格控制钢板的开轧及终轧温度,保证终轧温度在 870℃~ 890℃之间,并以型钢升温、降温对应的膨胀曲线作为 依据,同时结合TTT 和 CCT 曲线,明确相变点,分析样品性能 与组织物。结果显示,方案A 和B 的热处理强度与标准强度上限 接近,而方案 C 的热处理强度高于上限 ;在冲击韧性方面,方案 A 和 C 的平均冲击值均超过230J,样品在试验中存在非均匀组织 或碳化物聚集的情况。为确保型钢的冲击韧性和拉伸强度指标 达到要求, 建议有关人员对型钢的组织比例进行调控, 并严格按 照方案B 对型钢进行热处理。
作为典型的低合金钢,14Cr1MoR 大厚度钢现已在氨合成 塔、气化炉等领域得到广泛运用。考虑到该类型钢需要长期处于 高压且高温的恶劣环境下,如何提高其性能并延长其寿命便成 为人们关注的焦点。研究表明,该类型钢冲击韧性、拉伸强度间 的匹配程度,通常会给其性能产生直接影响,因此,要想做到大 规模生产优质型钢, 关键是要以既有热处理制度为基础, 对全新 制度及工艺进行开发, 这同时也是本文所讨论的主要内容, 有关 人员应对此引起重视。
1 项目提出背景与热处理质量问题
1.1 背景说明
随着“十四五”规划的开启,煤化工产业进入转型关键期。 在强调大型化的当下,国内企业生产的油化产品总数持续增加, 基本能够满足市场需求。这一转变使得产能面临同质化、规模小 和成本高等问题,并面临被淘汰的命运。新形势下,油化企业想 要抢占先机,关键是要将工作重心放在技术研发上。受技术升 级影响, 生产所使用的设备逐渐呈现出复杂化、大型化的发展趋 势。只有掌握大规模生产性能、品质及附加值理想的钢板制造方 法,企业才能顺利走出困境。以煤化工所用型钢为例,客户对型 钢厚度、模焊制度以及冲击韧性提出了极高的要求。少数客户要 求模焊时长达到 30h,升降温的速度不得低于 30℃ /h,产品装出 炉温度应在 100℃或以上。此外,还要求冲击温度的下限不得低 于 -28℃。按照淬火结合回火、冷却结合回火等既有热处理制度 所生产的型钢,虽然其冲击韧性、拉伸强度基本能够得到保证,但仍然存在性能波动幅度过大或无法达到行业标准的情况。根 本原因在于轧制等环节无法保证组织均匀。由此可见, 围绕热处 理制度展开讨论, 确定既能够保证产品质量, 又可以控制产品加 工成本的全新热处理制度很有必要。只有这样, 企业竞争力得到 提高, 行业才能得到稳定且持续地发展。
1.2 问题描述
据统计,2021 年所生产板厚超过 100mm 的 14Cr1MoR 大厚 度钢的冲击、拉伸性能达标率约为 85%,相关质量问题主要表现 在以下方面 :
其一, 冲击温度≤ 18℃时, 型钢冲击值未能达到行业标准。
其二,指定批次型钢拉伸强度未达到行业标准,模焊强度最 大值仍未能达到规定下限, 无法满足生产顺行等要求。
分析不达标型钢金相组织能够发现,虽然钢板多为回火组 织,不同型钢的组织形态却存在明显差别。其中,一部分样品的 基体表面遍布非均匀组织,该类组织多形成于淬火、轧制环节, 通常会对型钢冲击韧性产生不良影响 ;另外一部分样品的基体 表面遍布碳化物颗粒,随着该类物质大量聚集,型钢冲击韧性、 整体强度均会受到影响。正常情况下, 不达标型钢断口均分为两 个区域。为准确掌握碳化物分布与型钢冲击性能的关系, 研究人 员选择利用扫描电镜观察断口形貌。结果表明, 以上区域起裂处 均存在的碳化物, 其中, 三晶粒相交区域碳化物所产生影响最为 显著。
由此可见,断口起裂及扩展都会受到碳化物影响。若晶界聚 集大量碳化物, 型钢冲击性将无法达到行业标准, 导致该情况出 现的原因如下 :裂纹多起源于晶界碳化物,沿碳化物向其他区 域延伸。一旦裂纹穿透晶界,该区域便会出现脆性断裂,致使冲 击功大幅降低。型钢性能必然会受到影响。综上,淬火、轧制环 节所形成非均匀组织、基体、晶界所存在碳化物均会在不同程度 上影响型钢性能, 使型钢冲击韧性、整体强度的匹配程度难以达 到预期。
2 试验前准备
通过分析可知,非均匀组织、碳化物与型钢性能匹配程度密 切相关, 要想使热处理工艺发挥出应有作用, 既要对组织转变规 律进行研究,还要对碳化物析出与型钢性能间的关系加以了解, 鉴于此, 有关人员决定以既有热处理制度为落脚点, 对不同制度 给型钢产生的影响进行研究。
2.1 试验材料
为保证研究所确定热处理制度具有普适性及针对性,有关 人员指出应先对厚钢板进行热处理,再切取研究需要用到的样 品。生产钢板的步骤相对繁琐,通常包括①利用 100t 的电炉进 行粗炼 ;②利用LF 炉进行精炼 ;③进行为期 30min 的真空处 理 ;④模铸并清理, 锭身尺寸是 850×2500×3500mm ;⑤加热 轧制 ;⑥探伤 ;⑦淬火及回火 ;⑧切取样品。钢板开轧温度处 于 910℃~ 930℃之间,终轧温度处于 870℃~ 890℃间,轧后浇 水对应返红温度不得超过 700℃。根 据 GB 713-2014《 锅 炉 和 压 力 容 器 用 钢 板 》试 验 所 用 14Cr1MoR 钢板化学成分的质量分数应满足以下要求 : C ≤ 0.17%, Si 在 0.50% ~ 0.80% 之 间,Mn 在 0.40% ~ 0.65% 之 间,P ≤ 0.020%, S ≤ 0.010%, Cr 在 1.15% ~ 1.50% 之 间,Ni ≤ 0.30%, Mo 在 0.45% ~ 0.65% 之 间,C ≤ 0.30%。 试 验所用 14Cr1MoR 钢板的力学性能要求如下 :钢板厚度在 6mm ~ 100mm 间时, 拉伸试验 Rm 取值为 520MPa ~ 680MPa, ReL取值为 310MPa, 断后伸长≥ 19%, 冲击试验温度≥ 20℃, 冲 击吸收能量 47J。钢板厚度超过 100mm 时,拉伸试验Rm 取值改 为 510MPa ~ 670MPa, 对应 ReL 取值为 300MPa, 断后伸长率、 冲击试验温度、冲击吸收能量同上。-20℃及 -30℃工况下,横向 冲击功单一值和平均值均在 60J 以上。
2.2 试验设备
试验所用电阻炉的内腔容积是 450×550×850mm,炉膛内 表面的材质是碳化硅,选用该材质的原因在于其性能十分稳定, 通常不会与炉内物质发生反应。另外,该设备由电阻丝负责加 热,额定功率是 35kW。
3 试验方案与过程
有关人员以型钢升、降温对应膨胀曲线为依据,结合TTT 与 CCT 曲线,对具体相变点加以确定,前者的相变点处于 752℃~ 760℃间,后者的相变点在 880℃左右。在明确高温淬火 与较高温调控相结合的理念后,分别设计4 种方案,每种方案所 使用样品尺寸、性能完全相同。
方案A :首先,将样品置于 920℃环境下,保温 4h 后出炉空 冷 ;其次, 将样品置于 900℃环境下, 保温4h 后出炉水冷 ;最后, 将回火温度调整为 680℃,对样品进行为期 6h 的回火保温处理, 空冷并备用。方案B :首先,将样品置于 920℃环境下,保温 4h 后出炉空冷 ;其次,将样品置于 880℃环境下,保温4h 后出炉水 冷 ;最后,将回火温度调整为 670℃,对样品进行为期 7h 的回火 保温处理,空冷并备用。方案 C :首先,将样品置于 920℃环境 下,保温 4h 后出炉空冷 ;其次,将样品置于 860℃环境下,保温 4h 后出炉水冷 ;最后,将回火温度调整为 650℃,对样品进行为 期 5h 的回火保温处理, 空冷并备用。
实验结束后,再通过热处理与最大模焊制度相结合的方式,对另一组样品进行处理,具体方案如下 :先按照方案A ~ C 的 步骤分别处理样品, 再按照最大模焊制度二次处理样品, 样品装 出炉的温度在 350℃左右,加工过程中,升降温速度始终被控制 在约 55℃ /h,加工所得样品编号依次为④~⑥。
4 试验结果分析
4.1 性能分析
本项目中,有关人员以现行技术要求为依据,对样品拉伸性 能、横向冲击性能进行检验。拉伸试验采用WDW-100微机控制 电子万能试验机,冲击试验采用JBW-450CYD 摆锤冲击试验机 进行,A 至 C 分别需要用到 6 支冲击平行样、1 支拉伸平行样,其 中,-20℃及 -30℃平行样各 3 支。E、F、G、H 所需平行样类型及 数量同上。对冲击功、抗拉强度平均值进行计算可知,上述方案 中,A 及B 的热处理强度与标准强度上限较为接近,最大模焊强 度明显高于标准下限。C 的热处理强度在标准强度上限之上,受 最大模焊影响, 样品强度将降到标准强度下限, 整体波动幅度较 大,换言之,按照方案 C 生产型钢,将有一定概率发生型钢强度 无法达到行业标准下限的问题。在冲击韧性方面,A ~ C 的平均冲击值普遍>230J,但经 过最大模焊处理之后,样品冲击韧性将发生明显改变,以 -20℃ 工况为例,样品⑤的平均冲击值相对较高,约为 206J,可以达 到行业标准,A 及B 的平均冲击值次之,约为 150J,C 的平均冲 击值最低,仅能达到约 100J,同时存在< 100J 的单值。-30℃工 况下,样品①、②所表现出冲击韧性大致相同,对应平均值处 于 160J ~ 170J 间,C 的冲击韧性并不理想,平均值仅能达到约 100J,其中,存在 83J 的单值。由此可见, 按照方案C所生产型钢, 有较大概率发生冲击韧性不达标的问题, 这点要有所了解。
4.2 组织物分析
4.2.1 电镜组织
对比扫描电镜组织能够发现,按照不同方案所加工样品的 析出物, 通常存在一定的差别, 这是因为不同方案在碳化物转变 方面的表现有所不同,样品组织自然也有所不同。其中,样品② 碳化物呈现出弥散且均匀的分布状态,这对提高其冲击韧性具 有正面影响,其他样品则普遍存在非均匀组织或碳化物聚集的 情况。
4.2.2 显微组织
研究表明,按照不同方案加工的样品存在明显差异。在实验 室条件下,样品②晶粒度、组织细化程度最为理想。导致该情况 出现的原因主要是样品②一次淬火温度相对较高,可充分满足 奥氏体均匀化要求。加之样品经过保温处理并通过水冷的方式 降至室温,也具有细化晶粒的效果。B 的二次淬火温度在 880℃ 左右,在调配组织比例方面扮演重要角色。这里要明确一点,即 研究所用小型电炉的保温性和加热性较为理想。保温过程中, 炉 内温度浮动幅度往往不会超过 5℃。日常生产所使用的设备规模较大且性能并不稳定。若要进行大规模生产, 有关人员应将温度 再提升 30℃以确保生产作业得以有序推进。同样地,样品①经 过高温正火处理后其内部含有不均匀组织的原因主要是冷却环 节所使用的空冷工艺整体冷却强度不理想,使得组织内形成慢 冷组织。加之二次淬火温度相对较低,仅有 900℃,致使慢冷组 织得以保留, 最终以不均匀组织的形态存在于样品内部。需要注 意的是, 若淬火处理的温度较低, 将无法保证型钢轧态组织所具 有遗传效应被彻底消除。由此带来的问题便是组织内部存在块 状组织, 会对样品性能产生不良影响。作为铁素体和贝氏体所组 成的原始组织,仅凭借单一的热处理无法使轧态组织得到有效 消除。换言之,要想保证型钢冲击韧性达到行业标准,关键在于 对热处理制度进行创新,将组织遗传效应所产生的影响降至最 低。样品④所表现出的组织形貌极为典型。该制度强调先对样 品进行高温催化处理,再通过水冷的方式使样品温度下降至室 温。这样做不仅能够使轧态组织遗传得到消除, 还可以起到细化 晶粒的效果。二次淬火采取亚温淬火法,温度相对较低。通过该 方法所获得的组织为贝氏体和铁素体混合物。考虑到样品所含 铁素体较多, 并且铁素体普遍呈现出不规则或是长条状, 极易给 冲击韧性产生负面影响。因此, 按照该方案加工型钢虽然能够保 证其冲击韧性和拉伸强度达到行业标准,但型钢强度较易受到 长时间模焊影响而降低。与此同时, 其冲击性能也将受到影响。
5 最优热处理方法讨论
研究表明,要想使型钢冲击韧性和整体强度达到理想水平, 关键是要对组织比例进行科学调控。日常生产中,有关人员可 以按照方案B 进行加工,确保所生产的型钢组织细密且均匀。 同时,对析出物的分布加以控制也可以起到改善型钢性能的效 果。本文所讨论的型钢模焊温度多处于 675℃~ 690℃之间。将 型钢置于该温度下进行最大模焊处理,其原理与回火相似。经 过长时间模焊的型钢,其冲击韧性往往会出现明显降低。这是 因为长时间模焊会加快碳化物的转变速度,从而影响型钢性能。 14Cr1MoR大厚度钢的冲击韧性和整体强度均与此密切相关。回 火期间, 富碳奥氏体表面将析出大量含铬钼碳化物。碳化物聚集 形成相应渗碳体,渗碳体形成后将有少数碳化物转移到铁素体 和渗碳体相交区域。随着碳化物增多, 型钢冲击韧性将受到负面 影响。在此过程中,位错处和亚晶界还会有少量碳化物析出。考 虑到上述区域所析出碳化物具有细小且弥散的特点,除特殊情 况外,其对冲击韧性所带来的影响均可忽略不计。分析可知,最 大模焊与单一热处理的区别主要表现在以下方面 :经过最大模 态处理的样品,其晶内、晶界表面均存在Mo 和 Cr 碳化物,碳化 物析出量与处理时长的关系为正相关。另外, 最大模焊和单一热 处理所产生的析出相,其Mo 和 Cr 碳化物浓度均在现行技术要 求之上(即超过 1.5%)。其中,前者所产生的析出相的碳化物浓度更高。由此可见, 可给型钢冲击韧性和整体强度产生影响的因 素极多。要想改善型钢性能,一方面要了解碳化物析出的特点, 同时掌握其溶解规律。另一方面, 则需在日常生产中对相关参数 加以控制。
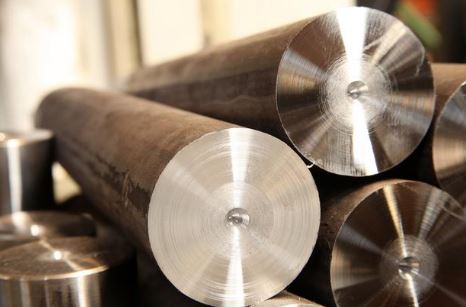
理想状态下,碳化物的析出顺序是①晶界,②晶内,要想使 析出物分布达到理想状态, 关键是要通过细化晶粒的方式, 对晶 界总面积进行增加。在细化晶粒方面, 实证有效的方法如下 :对 样品进行高温淬火处理, 通过持续加热的方式, 加快型钢奥氏体 化速度,确保其内部成分更加均匀,由此而带来的连锁反应,便 使碳化物、渗碳体快速溶解,晶内所含合金元素变得均匀。事实 证明,合理运用高温淬火法,可避免经过淬火处理的型钢,其组 织内部仍含有大量碳化物,由碳化物所转变的渗碳体总数自然 有所减少。此外,以下内容同样需要引起重视 :其一,奥氏体淬 透性与合金元素溶解程度的关系为正相关,充分溶解相关元素, 可使奥氏体表现出更为理想的淬透性,即使将型钢置于低冷速 条件下,型钢中心区域仍然能够转变成贝氏体。其二,在对正火 过程加以控制时, 有关人员应将重心放在冷却速度上, 通过增加 冷却速度的方式, 使贝氏体所含位错、亚结构总数得到大幅度增 加,为分离转变创造良好条件, 冲击韧性所受到影响自然能够得 到控制。分析试验所得结果可知,A ~ C对一次淬火进行保温的 时长均为 4h,晶粒细度主要取决于淬火温度,其中,920℃水冷 的影响最为显著,其次是 900℃水冷,最后是空冷,这表示对型 钢进行 920℃水冷处理,通常可取得较为理想的组织细化效果, 析出物的分布自然更加弥散且均匀。综上,实验室条件下,方案 B在控制析出物分布、调整组织比例方面所取得效果最为理想, 方案A 次之。而按照方案 C所加工样品的组织性能、冲击韧性均 无法达到行业标准。
6 结语
现将本研究所得结论归纳如下 :首先,导致 14Cr1MoR大厚 度钢冲击韧性、拉伸强度不匹配的原因有两点,一是淬火、轧制 环节产生非均匀组织,二是基体、晶界表面聚集大量碳化物。其 次,实验室条件下, 对型钢进行热处理的最佳制度是 920℃水冷、 880℃水冷与 670℃回火相结合,按照该方案加工型钢,不仅能 够确保型钢组织均匀,对应晶粒度达到 7 级,还能够对碳化物尺 寸加以控制,确保碳化物不超过200μm,并为后续溶解和析出碳 化物提供便利。最后,还要注意一点,即对型钢进行高温退火处 理时, 有关人员应对温度加以控制, 以免出现碳化物大量析出或 是快速长大的情况, 给型钢性能产生负面影响, 以此来保证全新 热处理制度所具有的优点能够在生产型钢的过程中得到充分发 挥。
关注SCI论文创作发表,寻求SCI论文修改润色、SCI论文代发表等服务支撑,请锁定SCI论文网!
文章出自SCI论文网转载请注明出处:https://www.lunwensci.com/ligonglunwen/66810.html