SCI论文(www.lunwensci.com):
摘要:本文以金属材料试样制备与产品研发工艺优化为研究方向,针对取样部位、取样方向对于试样拉伸性能的影响进行分析,从中发现从金属材料局部取样、沿与轧制方向平行的方向取样能够有效提高试样的屈服强度与断后伸长率。在此基础上,探讨机加工工艺参数与试样力学性能试验结果的相关性,研究结果表明需重点做好试样形状公差、表面粗糙度、残余应力、磨削与抛光方向、肩部过渡与非对称性处理以及取样、制样工艺的优化,严格遵循国家标准进行试样加工质量检验,从而为力学试验结果的准确性提供保障。
关键词:金属材料;取样方法;机加工工艺;拉伸试验;力学性能
当前金属材料试样在航空航天、汽车工业、装备制造业、医学等多个领域收获广泛应用价值,伴随工程材料研发技术的不断更新,对于材料制备质量与综合性能提出更高要求。现阶段在完成试样制备后,需开展多种力学性能试验进行试样性能指标的测试,围绕取样操作、机加工处理两个关键工序环节进行测试分析,判断上述因素对于试样力学性能试验结果的影响,为材料性能试验的可靠性提供保障。通过聚焦金属材料制备工艺与性能测试两个层面进行研究与分析,对于工程材料制备及试样选材设计优化具有重要现实意义。
1 试样制备工艺
在金属材料试样制备前,从一批金属材料产品中随机抽选一产品作为子样,切取部分试料经预处理后作为样坯,完成取样操作。随后进入制样环节,对样坯分别采取车、铣、刨、磨等加工方式进行机加工处理,保证满足相关技术指标要求及验收标准,且不会破坏、影响金属材料性能,保证机加工精度达标,由此完成试样的制备。
2 取样方法
2.1 取样部位对拉伸试验的影响
取样作为试样制备的前置工艺,其操作要点体现在以下两方面:其一是取样部位,通常金属材料中心部位的性能相对偏低;其二是取样方向,沿纵向取样可使试样性能相对更优。同时,在冷、热变形加工过程中,金属材料侧重于向主变形方向流动,加之原材料内部冶金缺陷、加热或散热条件及其他工艺因素等,均可能导致金属材料在变形量、缺陷分布与金相组织上存在不均匀问题,由此引发试样的力学性能差异。将25#圆钢、25#槽钢作为测试对象,对取样部位与拉伸试验的相关性进行比较分析。
(1)在圆钢测试上,首先对φ50mm轧制圆钢执行取样操作,从中心部位取试料测得抗拉强度为507MPa、断后伸长率为31.4%,从1/4处取试料测得屈服强度为521MPa、断后伸长率为31.9%;其次对φ50mm冷拉圆钢执行取样操作,分别从中心部位和1/4处切取试料,测得屈服强度分别为520MPa和523MPa,断后伸长率均为31.5%;最后对φ60mm冷拉圆钢执行取样操作,分别从中心部位和1/4处切取试料,测得屈服强度分别为597MPa和618MPa,断后伸长率依次为11.3%和12.3%。从中可以看出,从试样中心部位取样测得的屈服强度相对偏低,断后伸长率无明显差别。
(2)在槽钢测试上,分别取槽钢腰部1/6、1/4、1/3、1/2和2/3五处进行毛坯件拉伸性能测试,测得其屈服强度分别为441MPa、439MPa、474MPa、489MPa和464MPa,抗拉强度分别为332MPa、348MPa、377MPa、380MPa和367MPa,断后伸长率依次为33.0%、32.0%、29.7%、29.5%和30.0%。在此基础上,取槽钢腿部1/3、2/3两处进行拉伸性能测试,测得其屈服强度分别为444MPa和440MPa,抗拉强度分别为355MPa和325MPa,断后伸长率分别为30.5%和33.0%。从中可以看出,取样部位的变化同样对于毛坯件拉伸性能具有不同程度影响,其中从腰部1/4处取样和从腿部1/3处取样后的力学性能测试结果基本满足GB/T2975-2018标准要求。
2.2 取样方向对拉伸试验的影响
针对试样取样方向与拉伸性能测试的相关性进行分析,取薄板金属材料进行测试,观察铁素体-珠光体带状组织(P-F)与回火温度分别在400°F、800°F工艺条件下M(400)-F、M (800)-F两种铁素体-珠光体带状组织的拉伸试验结果。当沿与轧制方向平行的方向进行取样时,测得P-F、M(400)-F、M (800)-F的屈服强度分别为477MPa、993MPa和732MPa,抗拉强度分别为307MPa、625MPa和466MPa,断面收缩率分别为57%、16%和41%;当沿与轧制方向平行的方向取样时,测得三种状态下屈服强度分别为432MPa、897MPa和579MPa,抗拉强度分别为279MPa、511MPa和409MPa,断面收缩率分别为13%、4%和10%。将纵向、横向试样的拉伸试验结果进行比较,从中可以看出纵向试样的力学强度、塑性指标均显著优于横向试样,由此确定沿轧制平行方向取样为最佳工艺条件。
3 机加工工艺
3.1 形状公差对应变测试的影响
对不同横截面金属材料试样进行机加工处理时,可能导致试样出现两端大小不同、中间部位过小或过大等问题,对此分别选取圆形、矩形两类横截面试验进行应变测试分析:
(1)圆形横截面试样,此类试样在加工过程中极易出现两端大小不一致的问题,使试样存在形状公差,并由此引发应变测定结果的变化。
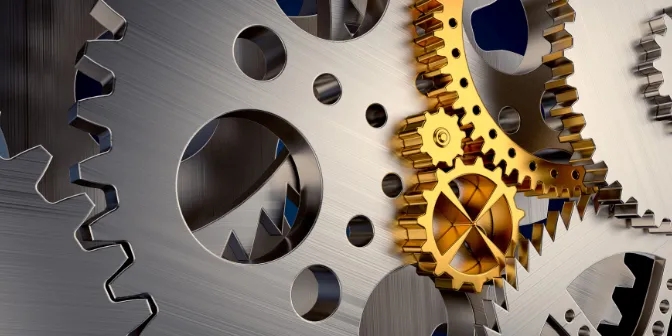
分别取直径为3mm、3mm~6mm、6mm~10mm、10mm~18mm、18mm~30mm五种圆形横截面试样,各试样的形状公差控制在0.02mm~0.05mm范围内,等效标距依次设定为0.967L0、0.952L0~0.975L0、0.967L0~0.980L0、0.980L0~0.989L0以及0.986L0~0.992L0,五种试样的应变误差测定结果分别为-3.4%、-5.0%~-2.6%、-3.4%~-2.0%、-2.0%~-1.1%以及-1.4%~-1.1%。从中可以看出,圆形横截面试样的五种形状公差对应的应变误差数值相近,最大相对误差控制在-5.0%左右,符合常用尺寸试样的误差限值要求。
(2)矩形横截面试样,此类试样在原始标距范围内厚度均匀,但沿原始标距方向在试样宽度上存在一定形状公差,仍以两端大小不一致为主要表现形式。
分别取宽度为3mm、3mm~6mm、6mm~10mm、10mm~18mm、18mm~30mm、30mm~50mm六种矩形横截面试样,以两试样为一组划分为三组,各组试样的形状公差分别对应0.05mm、0.10mm和0.20mm,等效标距依次为:
-0.960L0,-0.960L0~-0,980L0-0.960L0~-0.975L0,-0.975L0~-0.986L0,-0.973L0~-0.984L0,-0.984L0~-0.990L0,
六种试样的应变误差测定结果依次为:
-4.2%、-4.2%~-2.0%、-4.2%~-2.6%、-2.6%~-1.4%、-2.8%~-1.6%以及-1.6%~-1.0%。
从中可以看出,不同宽度的矩形横截面试样因形状公差引发的应变测定误差均为负值,最大应变误差为-4.2%,说明形状公差的增大将使试样的断后伸长率、均匀伸长率数值均明显下降,因此需参考GB/T288-2013标准做好试样外形尺寸的严格控制,优化机加工工艺水平。
3.2 表面粗糙度对拉伸试验的影响
不同金属材料经机加工处理后期表面粗糙度存在一定差异,以塑性较差的金属材料试样为例,当试样表面粗糙度增大时,其强度、塑性指标与疲劳极限均呈下降趋势。
以Q460钢材料为例,首先针对试样表面粗糙度与抗拉强度的相关性进行分析,采用四面机加工工艺进行试样的加工,对于表面粗糙度分别为0.4μm、0.6μm、0.8μm、1.0μm和1.2μm的五种矩形横截面试样进行拉伸试验,测得各试样的抗拉强度依次为1250MPa、1245MPa、1240MPa、1225MPa和1150MPa。从中可以看出,当试样表面粗糙度小于0.8μm时,抗拉强度呈逐渐增大趋势。
其次针对试样表面粗糙度与塑性指标的相关性进行分析,同样对五种表面粗糙度不同的矩形横截面试样进行拉伸试验,测得其断后伸长率分别为12.5%、12.5%、12.5%、12.0%和11.5%。从中可以看出,伴随试样表面粗糙度的逐步增大,其断后伸长率数值呈现出不断下降趋势,说明粗糙度增大将使试样塑性指标裂化,需将试样表面粗糙度控制在0.8μm以内。
最后针对试样表面粗糙度与疲劳极限的相关性进行分析,以30crNi4MoA高强度高韧性结构钢作为原材料,取机加工后表面粗糙度分别为0.8μm和0.4μm的两种试样进行旋转弯曲试验,测得二者疲劳极限分别为292Mpa和312MPa,差值为20MPa。从中可以发现,伴随表面粗糙度的增加,试样的疲劳极限呈下降趋势。
3.3 残余应力、磨削和抛光方向对疲劳试验的影响
机加工涉及的工序环节较多、工艺操作相对复杂,诸如试样是否均匀冷却、进刀量大小等均有可能使其表面产生残余应力,同时在对试样进行旋转弯曲试验的过程中也可能引发残余应力增大。针对残余应力与疲劳极限的相关性进行分析,将试样表面粗糙度统一设定为0.4μm,当试样表面压缩残余应力为-10MPa时,对应的疲劳极限为570MPa;残余应力取值为-120MPa时,试样疲劳极限为578MPa,差值为8MPa;残余应力取值为-430MPa时,试样疲劳极限为605MPa,差值为35MPa。从中可以看出,伴随试样表面残余应力增大,其疲劳极限也呈同步增大趋势。
针对磨削、抛光工艺与试样疲劳极限的相关性进行分析,首先以18CrNi4WA钢材为例,采用横磨纵抛光、纵磨纵抛光工艺对应的试样表面粗糙度分别为0.1μm和0.05μm,疲劳极限分别为559MPa和597MPa。从中可以看出,选用纵磨工艺有助于提升试样的疲劳极限。其次以60Si2Mn弹簧钢材料为例,分别采用横磨纵抛光、横磨横抛光工艺进行试样加工,两试样的表面粗糙度均为0.2μm,疲劳极限分别为555MPa和460MPa。从中可以看出,在同样选用横磨加工的条件下,采用纵抛光工艺可使试样的疲劳性能同比提升20%左右。最后以LC4铝合金材料为例,分别采用纵磨纵抛光、横磨纵抛光工艺进行推论检验,两试样表面粗糙度分别为0.8μm和0.4μm,疲劳极限分别为203Mpa和189Mpa。从中可以看出,在保持抛光工艺不变的条件下,纵磨工艺可使试样的疲劳极限明显提升,且在纵磨工艺下试样表面粗糙度较大,因此使得试样性能同比提升约7%。
3.4 肩部过渡和非对称性对屈服极限试验、拉伸试验的影响
在机加工环节制备的试样分为带头、不带头两种类型,带头试样在平行部分与夹持部分之间设有肩部过渡区r,现行标准要求矩形横截面薄板试样的r值不小于20mm、板材或扁材试样的r值不小于12mm。当机加工工艺处理后的试样规格参数无法满足标准要求时,经由拉伸试验测得的试样上屈服强度数值保持在较低水平,说明伴随r值的增大,过渡区域的缓和上屈服强度呈现出显著增大趋势。针对肩部过渡区大小与试样上屈服强度的相关性进行分析,以宽20mm、厚2mm的低碳钢材料为例,取r值分别为8mm、15mm、20mm、30mm、40mm的五种试样进行拉伸试验,测得各试样的上屈服强度分别为250MPa、275MPa、295MPa、320MPa和325MPa。从中可以看出,伴随试样肩部过渡值的逐步增大,其上屈服强度呈现出同步增大趋势,其中当r值不足20mm时,上屈服强度的增长速度较快;当r值达到20mm及以上时,上屈服强度的增长速度开始减缓,最终达到稳定状态。
与此同时,在机加工过程中带头试样肩部为对称、非对称两种状态时,其拉伸试验结果存在一定差异。其中在带头试样肩部处于非对称性状态的情况下,受应力分布特征的影响,在机加工过程中试样将在偏心力作用下局部出现附加弯曲应力,导致带头试样在拉伸过程中施力线与原轴线重合,由此进一步增大拉伸试验结果的误差。为解决此问题,宜选用QXK6040C型数控双开肩铣床投入试样机加工环节,在试样加工过程中保证两面进刀、出刀的同步进行,有效防范试样局部弯曲应力过大,保证拉伸试验结果的精确度。
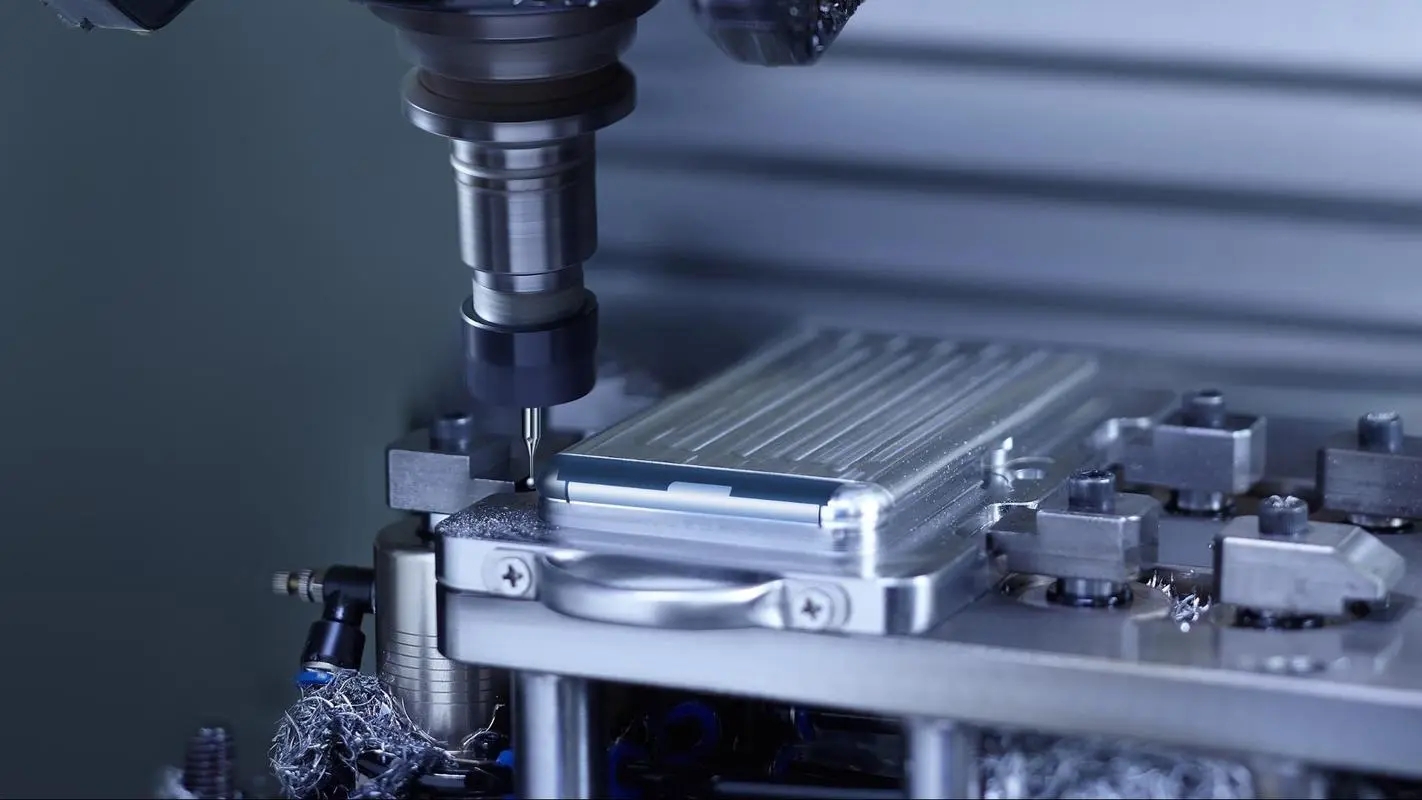
3.5 取样与制样工艺对冲击试验的影响
当前金属材料试样普遍采用轧制工艺制造成型,但在轧制加工过程中将使材料中生成纤维组织,一定程度上影响到冲击试验吸收功的效果,其首要决定性因素在于取样方向。针对取样方向与冲击试验的相关性进行分析,当沿与轧制方向平行的方向进行取样、沿垂直方向开设缺口时,测得试样冲击吸收功数值相对偏高;当沿与轧制方向垂直方向取样、沿平行方向开设缺口时,测得试样冲击吸收功保持较低水平。
与此同时,选用冲击试样机开展试样工艺验证,在此过程中诸如缺口的深度、角度以及根部的曲率半径、表面粗糙度等指标均会影响到试样缺口部位的应力分布特征,进而对缺口冲击性能产生影响。对此选取缺口深度、缺口根部曲率半径两项指标进行研究分析:
针对缺口深度与冲击试验的相关性进行分析,根据现行标准要求,当缺口深度为2.0±0.025mm时,高、中、低能量的三类试样对应的冲击吸收功分别为103±5.2J、60.3±3.0J和16.9±1.4J;在测试指标设计上,当缺口深度分别取值为2.14mm、2.05mm、1.98mm和1.89mm时,高能量试样的冲击吸收功分别为98.0J、101.9J、104.2J和108.0J,中能量试样的冲击吸收功分别为56.1J、57.3J、61.5J和62.5J,低能量试样的冲击吸收功分别为15.6J、16.9J、17.3J和17.5J。从中可以看出,不同能量等级试样的缺口深度增大均会使其冲击吸收功数值呈现出显著减小趋势。在此基础上,对于试样缺口深度增长率与冲击试验的相关性进行分析,从中发现当缺口深度同比增大13%时,能量由高到低的三类试样冲击吸收功由9.3%下降至10.9%,由此可以看出低能量试样的缺口深度对其冲击试验结果的影响明显偏高。
针对缺口曲率半径与冲击试验结果的相关性进行分析,根据现行标准要求,当缺口根部曲率半径为0.25±0.025mm时,高、中、低能量的三类试样对应的冲击吸收功分别为103±5.2J、60.3±3.0J和16.9±1.4J;在测试指标设计上,将缺口根部曲率半径分别取值为0.14mm、0.28mm和0.39mm,测得高能量试样的冲击吸收功分别为98.1J、108.3J和108.6J,中能量试样的冲击吸收功分别为56.6J、63.4J和64.4J,低能量试样的冲击吸收功分别为14.7J、18.4J和21.5J。从中可以看出,不同能量等级试样缺口根部曲率半径的增大均会使其冲击吸收功同步增大。
此外,当试样的缺口角度、表面粗糙度等指标增大后,将使其冲击吸收功呈下降趋势;当试样尺寸增大后,使试样在后续冲击试验过程中的塑性变形体积扩大,由此冲击吸收功呈增加趋势,但与此同时也将扩大对试样的约束程度,可能导致试样出现脆性断裂,因此需注意控制好试样尺寸增量,避免对冲击试验结果构成负面影响。
4 制样工艺优化及加工质量检验
4.1 制样工艺优化
由于金属材料试样制备的关键在于机加工处理环节,为保证试样和产品品质、性能符合规范要求,还需重点聚焦制样工艺进行优化设计方案的编制。例如在车削粗加工环节,需控制切削深度、走刀量等工艺参数;在铣削环节,应调节铣削速度、进刀量以及表面精加工余量;在磨削环节,应注意控制热处理工艺、材料选型等关键指标,以标称尺寸为参照,当超出标称尺寸0.1mm时将磨削深度控制在0.03mm,当超出标称尺寸0.025mm时将磨削深度控制在0.005mm左右,并在磨削过程中做好试样的冷却处理,选用水基溶液使试样得到充分冷却,进一步提升磨削环节的加工精度;在表面抛光环节,将试样加工至预设直径后,选用细砂纸沿试样轴向进行充分打磨,依托纵向抛光处理保证试样表面粗糙度符合标准要求,且疲劳极限测试结果达标,消除表面残余应力、优化试样表面质量。
4.2 加工质量检验
待完成加工工艺优化后,需针对试样机的加工效果进行检验,对此可围绕以下三个层面入手。
首先从试样表面质量入手,分别选用粗糙度测试仪、X射线衍射应力测试仪、显微硬度计等测量仪器设备进行试样表面粗糙度、压缩残余应力以及硬度等质量指标的测定,并与国标值进行比较,保证试样表面质量达标。
其次从试样内部质量入手,聚焦金属材料试样的微观应力、金相变化、内部组织结构等层面进行技术指标的测定,借此检验试样内部质量及性能是否合乎标准,从而将试样机加工处理环节对于力学性能测试结果的影响降至最低。
最后从试样开设缺口质量入手,以试样表面开设V型缺口为例,主要围绕以下三个方面入手:①缺口深度,现行标准规定将缺口深度控制在2mm,对此可采用放大图方法进行缺口深度的检验,以圆弧定点为基准对试样缺口沿垂直方向的长度进行探测,分别在试样顶部与底部两端设置基准点,取基准点测量结果进行差值计算,保证将缺口深度的最大偏差度控制在允许范围内,并提高测量结果的精确度;②缺口根部曲率半径,当前主要选用光学投影仪进行试样缺口根部半径的检验,先利用放大图法进行缺口根部位置的放大处理,随后将放大图像置于投影仪上进行直观察看,观察缺口根部相切圆的圆弧底点,判断圆弧底部是否能够与标准重合,用于完成对曲率半径是否达标的准确判断;③缺口角度,在上述测试中对于缺口角度并无深入分析,其主要原因在于缺口角度不会对试样力学性能测试结果产生较大影响,但缺口角度仍会影响到试样质量及性能,以往主要采用公差放大图方法进行缺口全角度公差的检查,原方法要求将全角度公差控制在±2°范围内,对此需对原方法做出改进,将半角度的上限、下限分别进行缩小、扩大,借此使缺口角度的误差控制在48°±2°范围内,保证测量结果的精确度及试样品质。
5 结论
通过选取不同金属材料进行制样工艺流程的分析,分别对取样方法、机加工工艺与试样力学性能试验的相关性进行测试与分析,最终明确取样部位、取样方向对于金属材料试样屈服强度、断后伸长率两项力学性能的影响,以及形状公差、表面粗糙度、残余应力、磨削和抛光方向、肩部过渡及非对称性处理、取样和制样工艺与试样力学性能的关联。将上述试验过程中提炼出的工艺要点进行总结,能够为金属材料制样加工质量与力学性能试验准确度的提升提供良好示范意义。
关注SCI论文创作发表,寻求SCI论文修改润色、SCI论文代发表等服务支撑,请锁定SCI论文网!
文章出自SCI论文网转载请注明出处:https://www.lunwensci.com/ligonglunwen/48295.html