SCI论文(www.lunwensci.com):
摘要:在先进制造业发展战略的推动下,广大制造企业纷纷将新一代信息技术应用到先进制造的关键业务领域。基于此,以某柔性制造系统为例,基于数字孪生技术,按1∶1的比例构建该柔性制造系统的数字模型,使实体设备和数字模型的功能相同。系统测试结果表明:利用该数字模型可在柔性制造系统建设前进行虚拟调试,迭代优化并最终获得最佳建设方案;也可以在柔性制造系统的运行过程中实时监控实体设备,实时了解各设备的运行状态。
关键词:数字孪生;柔性制造;虚实融合;实际应用
Digital Twin Modeling and Application in Flexible Manufacturing System
Yan Hailan1,Shang Poli1,Yang Yalong2
(1.Lanzhou Petrochemical Vocational and Technical University,Lanzhou 730060,China;2.Lanzhou Institute of modern physics,Lanzhou 730000,China)
Abstract:Driven by the development strategy of advanced manufacturing,the majority of manufacturing enterprises have applied the new generation of information technology to the key business areas of advanced manufacturing.Based on this,a flexible manufacturing system was taken as an example.Based on digital twin technology,the digital model of the flexible manufacturing system was constructed at the ratio of 1:1,so that the physical equipment and the digital model had the same function.The system test results show that the digital model can be used for virtual debugging,iterative optimization and finally obtain the best construction scheme before the construction of FMS,which can also monitor the physical equipment in real time during the operation of FMS to understand the running status of each equipment in real time.
Key words:digital twin;flexible manufacturing;fusion of virtual and real;practical application
0引言
德国的“工业4.0”、日本的“重振制造业”等先进的制造业发展战略,旨在通过提高操作技术的自动化程度,实现制造业的智能化发展[1]。我国的广大制造企业也在“中国制造2025”、两化融合及“互联网+”等国家战略的推动下,将新一代信息技术应用到先进制造的关键业务领域,如管理、生产、服务和生产等,进而有效提升了企业综合竞争力[2]。但随着市场的个性化需求日益增长,制造企业的柔性化定制生产普遍存在着物流规划不合理、生产能力评估不充分、工艺布局不合理和质量稳定性不足等问题。数字孪生(Digital Twin)技术[3]将虚拟空间和物理空间结合起来,在虚拟空间再现真实生产制造场景,是企业柔性化制造中不可或缺的技术[4-5]。
2003年Michael Grieves教授首先对数字孪生进行了定义,即“孪生体”[6]指所有用来模拟物理产品状态的模型或样机。然而这一概念在当时没有得到进一步的发展,直到2010年美国国家航天局和美国空军提出了一种多概率、多物理场、多尺度的未来飞行器数字孪生模型[7]。2011年Michael Grieves教授对数字孪生[8]又给出了更详细的解释,它包括:实体产品和虚拟产品,以及两者之间进行信息和数据交互的通道。数字孪生的特征为:“实时/准实时”、“双向”和“全生命周期”。数字孪生[9-11]是一种集成多尺度、多物理量、多学科和多概率的仿真过程,在虚拟空间中利用传感器更新、运行历史、物理模型等数据实现映射,进而监控该实体设备的运行过程。
本文引入数字孪生技术,构建柔性制造系统的数字孪生模型。利用该数字孪生模型对建设前的方案进行虚拟仿真和调试,验证其合理性。并通过反复调整和迭代优化建设前的方案,可很大程度上缩短柔性制造系统设计、建设和投产的时间。利用数字孪生还可以在柔性制造系统建设运行时对实体设备进行实时监控,了解各设备的运行状态。
1基于数字孪生的柔性制造系统总体架构设计
1.1系统功能
柔性制造系统数字孪生模型可实现以下功能。
(1)评估柔性制造系统的性能
柔性制造的数字孪生系统应该对工件的到位信号、工件的合格率信号、工件的材质颜色等信号、气缸的到位信号、限位信号等信号进行实时监控,对超范围的参数进行提醒和报警。并通过系统的稳定度、系统的精确率和产品的合格率等,对生产系统的性能情况进行评估。
(2)制定并优化柔性制造系统的运行策略
数字孪生体与物理实体之间的双向作用,可为柔性制造系统运行策略制定提供有效的信息支持。即将物理实体的参与设备、运行约束条件、动作时序等信息作用于系统数字孪生体,并在数字孪生体上进行调试运行,通过不断迭代优化制定柔性制造系统的最佳运行策略。
(3)模拟故障状态与快速推演故障预案
数字孪生体可用于模拟故障状态,即通过改变数字孪生体的运行时序或参数。在数字孪生体的模拟故障状态下,可快速仿真模拟已经制定好的故障预案,判断故障预案的有效性和可行性。
1.2总体架构
柔性制造系统的数字孪生模型总体架构如图1所示,包括:数字孪生层、服务应用层及物理层。

图1总体架构
物理层主要由电气子系统、控制子系统和机械子系统3大部分组成。机械子系统由加工单元(钻床、铣床)、立体仓库(原料库、成品库、废品库)、龙门吊、视觉比对单元、热处理单元和装配加工单元等组成。还包括每个单元及整体的动作过程。电气子系统利用传感器采集工业现场信息,并保存到控制子系统的存储器中,控制子系统执行程序,进而驱动机械子系统按约束条件运行。
数字孪生模型包括数据模型、逻辑模型和几何模型。数据模型主要是将物理模型中的传感器信号、状态信号等映射到数字孪生模型中。逻辑模型用于映射物理层的实际运动过程,转化为数字孪生层的运动行为。几何模型,保证数字孪生模型与实际柔性制造系统在颜色、材质属性、形状、尺寸大小等方面具有高相似度。
服务层主要由远程控制和同步仿真两部分组成。同步仿真可以对物理系统的运行状态实时监控,作为性能评估的参考。远程控制则是通过数字孪生系统发送信号控制实际系统,实现反向控制,用于异常处理。物理层和数据孪生层是通过WiFi或以太网通行完成信息交互,并利用数据库存储或读取数据。
2柔性制造数字孪生关键技术
2.1数据感知和传输
近年来,随着传感器性能的逐渐提升,新型的传感器具有耐腐蚀、抗高温、采样频率高、采集数据大量增加等特点,柔性制造系统利用这些传感器将大量的相关数据提供给数字孪生体。因此,传感器的性能决定了数字孪生体的最终效果,这些新型的传感器为数字孪生提供保障。
传感器采集的信号主要有两种,一是开关量信号,二是模拟量信号。可通过可编程逻辑控制器(PLC)系统、分布式控制(DCS)系统等进行采集这些传感器信号。而这两种信号的采样周期不一样,通常模拟量信号的采样周期为分钟级、开关量信号的采样周期为秒级甚至毫秒级。因此,为了解决这些问题学者们采用了各种方法。如对概率主元分(PPCA)[12]等概率框架下的统计学习方法进行集成,对二采样率数据使用因子分析(FA)[13]。对多采样率数据利用多个卡尔曼滤波器进行信息融合[14]等。以及对完成自动化的数据利用TOSCA将分析算法与数据集成相互关联起来[15]。将图像、文本转换为向量表达形式的结构化数据,从而进行建模的方法也可作为借鉴应用于工业中。
物理实体与孪生模型间数据的传输是通过第五代移动通信网络(5G)进行传输的。5G因其大带宽、低延时、低功耗等特点,是实现数字孪生的必要技术。
2.2模型构建
柔性制造的数字孪生系统需真实、全面、综合的反映物理系统。本文对孪生模型的构建主要从逻辑模型、数据模型和几何模型3个方面进行了详细介绍。
(1)通过建立几何模型,保证数字孪生模型与实际柔性制造系统在颜色、材质属性、形状、尺寸大小等方面具有高相似度。本文采用SolidWorks软件进行三维建模。SolidWorks软件包括零件建模、模具设计、装配设计和运动仿真等,是非常优秀的三维设计软件。功能强大、易学易用、技术创新是SolidWorks软件的3大特点。在建模时需要对三维模型进行简化处理,保留主要部件如运动轴、工件、电机、热处理装置等,简化与仿真无关的部件。为详细描述柔性制造系统属性参数,建模时将属性参数绑定到三维模型上。柔性制造系统的每个单元都可以看做多个部件通过某种约束条件有机的联系在一起,构成一个具有某种逻辑关系的运动系统。
(2)逻辑模型主要是用来建立与实体模型一致的动态加工过程,构建虚拟柔性制造系统。逻辑模型还要实现数字孪生模型的同步仿真和远程控制。为了使虚拟系统能准确模拟运行过程,需要将实体模型的各类代码,如梯形图等进行识别与解析,代码解析如图2所示。
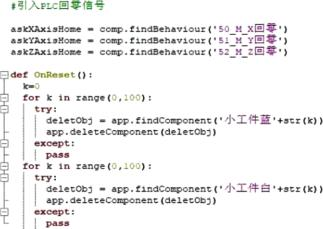
图2代码解析
(3)数据模型主要是将物理模型中的传感器信号、状态信号等映射到数字孪生模型中。由于本文利用PLC控制柔性制造系统,所以通过PLC采集传感器信号并暂存到输入映像寄存器和数据寄存器中,接着利用OPC通信建立与上位机OCTOPUZ的连接。OPC是目前使用比较广泛的基于标准的数据通信方法,它提取了数据发送设备(如PLC),和数据接收设备(如HMI)的执行细节,因此不需要了解彼此的本地通信协议和内部数据组织形式就可以进行数据交换。
数据接入流程如图3所示,首先确定从实体设备获得的数据信息,并确定数据映射关系。其次将数据映射关系和外部系统数据进行比较,确定从外部系统需要抽取的相关信息。然后将仿真数据和外部数据进行映射,匹配为对。若两者数据存在冲突,则消解冲突在虚拟系统中增加或删除相应的数据信号。若两者数据不存在冲突,则进行数据融合。

图3数据接入流程
3应用案例
本文以亚龙公司的YL-268柔性制造生产线为例,该生产线由立体仓库、加工单元、输送单元、视觉比对单元、热处理单元、装配加工单元等组成。其工艺流程为:从立体仓库的原料库中取出工件,搬至输送皮带上并运送至加工单元,加工完成后运送至视觉比对单元,比对不合格的工件直接运送至废品库,比对合格的工件运送至热处理单元进行加热和冷却处理,处理完成后运送至装配单元进行装配,装配完成后运送至成品库。
明确了柔性制造系统的组成和工作流程后,再明确柔性制造系统各个单元机理模型、可获取的数据、新增转化数据等。最后制定该柔性制造系统数字孪生体的需求分析和实现策略。
3.1柔性制造生产线数字建模
根据现有测量方法,完成对柔性制造系统实体对象的空间运动、几何结构、几何关联等几何属性的获取。利用SolidWorks实现柔性制造系统几何模型的构建。并对各设备空间几何模型进行匹配连接,
实现几何模型数字化精准复刻。在OCTOPUZ中导入已建立好的几何模型。PLC采集现场信息并保存在寄存器中,并与上位机OCTOPUZ进行OPC通信,实现对柔性制造系统外部信号的提取和映射,从而实现系统的控制和信息的采集。并使用Python语言在OCTOPUZ平台上开发包含模块功能和人机交互界面的系统程序进行验证。柔性制造系统的数字孪生建模效果如图4所示,为了得到良好的可视化效果,选择不同的帧时,将同一段代码执行20次运动仿真,从表1可知模型运动效果在13 ms左右时最好。并与物理实体设备相比较可知,柔性制造系统数字孪生模型在形状、模型的精细度等方面具有高保证度。

图4柔性制造系统的数字孪生建模效果
3.2模型测试验证
本文从模型的相对位置、数据采集量、模型响应延迟等方面来验证柔性制造控制系统数字孪生模型的性能。通过对数字孪生模型测量可知,每个部件都是1∶1还原实体模型部件,且每个单元部件的连接以及单元之间的连接完全与实体模型一致,满足实体模型的相对位置关系。实体设备与数字孪生模型采集到的信号,如轴的原点检测信号、轴的极限信号、气缸的极限信号等达到完全同步。且系统运行时,实际观测到的仿真运动无明显延迟。因此将数字孪生模型与生产系统相关联,实现同步运行、实时监控,可实现产品在设计、制造过程中的虚拟仿真,以提高产品的质量、生产效率和产品质量稳定性。
柔性制造系统的数字孪生模型可以为系统优化提供依据。一方面对数字孪生模型监测到的生产异常进行诊断,并按“问题分析——模型构建——算法设计——优化分析”的流程进行系统优化。另一方面利用聚类分析、关联分析、优化算法等方法,参考大数据的研究思路,对过程相关的数据进行分析,实现对生成过程的优化。
4结束语
将新一代信息技术应用到先进制造的关键业务领域,有效提升企业综合竞争力是必然趋势。数字孪生将被模拟对象和仿真模型融合起来,在虚拟空间再现真实生产制造场景,在柔性制造系统全生命周期数字化管理中发挥了重要作用。本文基于数字孪生技术,按1∶1的比例构建了柔性制造系统的数字模型,使实体设备和数字模型的功能相同。并利用该数字模型在柔性制造系统建设前进行虚拟调试,迭代优化并最终获得最佳建设方案。在柔性制造系统的运行过程中实时监控实体设备,实时了解各设备的运行状态。
参考文献:
[1]陶飞,刘蔚然,刘检华,等.数字孪生及其应用探究[J].计算机集成制造系统,2018,24(1):1-18.
[2]《机器人技术与应用》编辑部.中国制造强国之路—解析《中国制造2025》[J].机器人技术与应用,2015(3):21-30.
[3]Zhang Shou Rong.Energy-saving of iron-making system-the key point of technological progress in china's iron and steel in⁃dustry in the 21st century[J].Iron and steel,2005,40(5):1-4.
[4]郭亮,张煜.数字孪生在制造中的应用进展综述[J].机械科学与技术,2020,39(4):590-598.
[5]江海凡,丁国富,张剑.数字孪生车间演化机理及运行机制[J].中国机械工程,2020,31(7):824-832.
[6]Grirves M.Difitaltwin:manufacturing excellence through virtual factory replication[EB/OL].[2016-12-20].http://www.apriso.com/library/Whitepaper_Dr_.
[7]TUEGEL E J,INGRAFFEA A R,EASON T G,et al.Reengineering aircraft structural life prediction using a digital twin[J].Interna⁃tional Journal of Aerospace Engineering,2011:Article No.154798.
[8]Grieves M,Vickers J.Digital twin:mitigating unpredictable,unde⁃sirable emergent behavior in complex systems[M].Berlin:Spring⁃er-Verlag,2017.
[9]孙柏林,刘哲鸣.解耦数字孪生,赋能仪器仪表行业转型升级[J].仪器仪表用户,2020,27(2):89-91.
[10]杜明芳.基于数字孪生的智慧建筑系统集成研究[J].土木建筑工程信息技术,2020,12(6):44-48.
[11]吴淼,李瑞,王鹏江,等.基于数字孪生的综掘巷道并行工艺技术初步研究[J].煤炭学报,2020,45(S1):506-513.
[12]Ge Z,Song Z.Mixture bayesian regularization method of ppca for multimode process monitoring[J].Aiche Journal,2010,56(11):2838-2849.
[13]Fatehi A,Huang B.Kalman filtering approach to multirate infor⁃mation fusion in the presence of irregular sampling rate and variable measurement delay[J].Journal of Process Control,2017(53):15-25.
[14]Zimmermann M,Baumann F W,Falkenthal M.Automating the provisioning and integration of analytics tools with data resourc⁃es in industrial environments using opentosca[C]//Proceedings of the IEEE 21st International Enterprise Distributed Object Computing Workshop.Palais Quebec City,QC,Canada:IEEE,2017.
[15]Chang S,Han W,Tang J.Heterogeneous network embedding via deep architectures[C]//Proceedings of the 21th ACM SIGKDD Interntional Conference on Knowledge Discovery and Data Min⁃ing.New York,USA:ACM,2015.
关注SCI论文创作发表,寻求SCI论文修改润色、SCI论文代发表等服务支撑,请锁定SCI论文网!
文章出自SCI论文网转载请注明出处:https://www.lunwensci.com/ligonglunwen/47792.html