SCI论文(www.lunwensci.com):
摘要: 电厂球阀结构设计不合理是电厂生产效率降低、事故发生的重要因素, 为改善电厂球阀的结构设计, 对球阀结构的既往设 计流程、设计经验进行梳理。首先, 针对球阀结构设计中的球体半径、最小壁厚的设计方法进行介绍, 给出计算结果, 球体设计 半径 21.27 mm, 最小壁厚取 5 mm。其次, 就阀体最小壁厚进行一次薄膜应力、一次薄膜应力加弯曲应力校核, 校核结果满足设计 标准的要求。最后, 基于有限元理论对设计球阀阀口的强度进行性能仿真分析, 通过 Solidworks 构建球阀的几何模型, 有序完成三 维模型的构建、有限元方针条件的设定、材料属性的确定、智能网格的划分、施加约束与载荷等工作, 利用 ANSYS 软件验证其设 计强度。有限元仿真结果显示, 球体最大应力区的应力数值明显低于 WCB 材料的许用应力, 设计球阀阀门的强度性能稳定。
关键词:球阀; 电力系统; 结构设计; 强度校验; 仿真
Structural Design and Strength Performance Simulation of Power Plant Ball ValveWang Wei1, Li Yong2
( 1. Nuclear Industry Engineering Research and Design Co., Ltd., Yangjiang, Guangdong 529500, China;
2. Huizhou Branch of China Nuclear Industry 23 Construction Co., Ltd., Huizhou, Guangdong 516200, China)
Abstract: The unreasonable structural design of power plant ball valve is an important factor for the reduction of production efficiency and
accidents. In order to improve the structural design of power plant ball valve, the previous design process and design experience of ball valve
structure were combed. Firstly, the design method of sphere radius and minimum wall thickness in the structural design of ball valve was
introduced, and the calculation results were given. The sphere design radius was 21.27 mm and the minimum wall thickness was 5 mm.
Secondly, the primary membrane stress, primary membrane stress and bending stress were checked on the minimum wall thickness of the valve
body, and the check results met the requirements of the design standard. Finally, based on the finite element theory, the performance
simulation analysis of the strength of the designed ball valve port was carried out . The geometric model of the ball valve was constructed
through SolidWorks, the construction of three-dimensional model, the setting of finite element policy conditions, the determination of material
properties, the division of intelligent grid, the application of constraints and loads were completed in order, and the design strength was verified
by ANSYS software. The finite element simulation results show that the stress value in the maximum stress area of the ball is significantly lower
than the allowable stress of WCB material, and the strength performance of the designed ball valve is stable .
Key words: ball valve; power system; structural design; strength verification; simulation
0 引言
球阀是改变介质流向、分配流量、阻断流量的装 置, 其功能类似于开关、切断阀。在电厂生产中, 球阀 的应用极为广泛, 但由于运行环境的特殊性, 球阀需要 具备良好的耐高温、承受载荷能力, 这对球阀设计的材 料选取与强度性能校验提出了较高的技术性要求。本文 围绕电厂球阀的结构设计以及强度校验展开讨论, 从理 论基础看, 现阶段与电厂球阀的文献研究偏少, 研究方 向主要集中在球阀密封检测[1-3]、球阀内漏故障的设计改 进[4-5] 等方面, 罗利梅[6] 针对高温耐磨球阀的设计进行研 究, 从工作原理出发, 以保证阀门的密封、寿命等为目的, 对壁厚、密封力的综合计算方法进行了介绍, 并利 用公式法验算了阀杆的强度, 但未对球阀的强度性能进 行仿真分析; 杨熙翀等[7] 以球体、阀座的摩擦力矩计算 为着眼点, 以解决球阀出厂测试、运行异常等问题为目 标, 对球阀设计制造环节内部零件的质量控制进行了讨 论, 但并未给出系统的设计思路与校验方法。现有文献 从不同角度探讨了不同性能球阀的设计问题, 提出了球 阀设计软件的开发思路, 利用公式计算、对比试验等方 式给出了有益的建议, 而有关球阀结构设计中关键参数 的计算、校验与性能指标的校验方法则散见于各类文献 资料、专业著作中。对常规球阀设计任务, 阀口相关的计算工作可以通过沿用现有的材料力学理论以及简化处 理的经验公式来实现, 壁厚和压力的确定可以参照某些 经验系数, 各类文献得出的结论也能够提供有益的参考, 但在涉及到特种阀体的超临界、高参数问题时, 上述策 略将面临失效风险。为此, 本文拟从仿真分析的视角出 发, 审视球阀结构设计中的强度设计、应力分析问题, 希望提出一种有效的仿真分析策略, 解决特种阀体的设 计难题。
1 球阀结构设计
1.1 球体半径R 确定
设计球阀首先应确定球体外圆半径 R, 确定的依据 是球体通道直径和介质工作压力 P, 如图 1 所示。当 α =36° 时, sin α = , R = , 设计 DN=25 mm, 故实际设计尺寸应满足 R实际 ≥ R设计 = 21.27 mm。
球阀在达到密封时所需的密封面宽度如图 2 所示。
图 1 球阀球体半径确定 图 2 球阀密封面宽度
首先要以密封原料的许用比压作为根据, 通过必不 可少的密封面的比压公式, 可根据下式初步算出密封圈的宽度 bM:

( 1 )
如果采用聚四氟乙烯制作阀座密封圈, 则许用比压 为[q]=17.5 MPa; c 代表系数相关密封面材料, 针对聚四 氟乙烯 c=1.8, c 为密封条件已确定的情况下, 参照的影 响系数为质压力对比压值, 针对聚四氟乙烯, k=0.9。把 以上数值代入式 (1), 经计算得:
bM = 0.027p2 + 0. 1 ( 2 )
上式中 p 为设计压力, 通常取公称压力 pN 数值的

, 经计算, bM=0. 11。
对于阀座密封圈, 用金属圈加固时, 许用挤压应力 可适当加大。因此无论球阀的状态是开启还是关闭, 球 体与密封面宽度都要大于 bM, L 代表两倍于密封面的宽 度 投 影 , 理 应 增 大 的 球 体 半 径 a 。 因 为

所以必须增加球体

该数值是满足球体密封的最小直径。例如加大球体强度以及球体直径的合理增加。将数据代入, 可以求得R实际

≥ +

= 21.35 mm, 为 方 便 计 算, 本 设 计 中 取 R实际 =21.5 mm。
1.2 球阀中体最小壁厚计算
依据 AP16D-2008 和 GB/T20173-2006 标准要求, 对 球阀的角焊缝强度有效系数取 0.75, 即是局部无损检 测。也就是中体和颈部的焊接, 属于角焊缝, 只能做表 面无损检测, 即 MT 或 PT, 不能做射线无损检测, 也不 能做超声波无损检测[8-9]。因此, 角焊缝的强度有效系 数才取 0.75, 也就是用加厚壁厚, 增加焊缝深度, 来弥 补由于焊缝不能进行全面 100% 的射线检测可能出现的 缺陷。
因此, 全焊接球阀中体和左、右体的最小壁厚的计算, 按 GB/T12224-2005 标准计算最小壁厚应为:

式中: tB 为考虑内压的最小计算壁厚, mm; pN 为公称压 力数值, 取 63; S 为应力系数, 取 48.3 MPa; DN 为阀体 中腔最大内径, 取 15 mm; E 为焊缝强度有效系数, 取 0.75; k 为系数, 当 pN=63 时, k=0.91; C1 为附加裕量, 由pN 和 DN 共同确定, 这里取 2.63 mm。
将数据代入可以计算得 tB =3.40 mm, 综合考虑在设 计时最小壁厚取 5 mm。
1.3 阀体最小壁厚校核
1.3.1 校核一次薄膜应力
通过介质压力对阀体的作用, 高应力区呈现在阀体 中腔与流道的连接的地方, 拐角区一次薄膜应力校核参 考 ASME III-NB 分卷的压力面积法[10]。
针对阀体一次薄膜整体的应力, 其所使用的标准计 算压力 Ps 需依据 ASME B16.34 插值获取与材料相关的压 力-温度 (260 ℃) 基准值:
Ps = P 1 - ( P 1 - P2 )(

) ( 4 )
其中, P1 =3.34 MPa, 为球阀原料 316Ti 在 250 ℃ 、 Class300 下的基准值; P2=3. 16 MPa, 为阀体材料 316Ti 在 250 ℃ 、Class300 下的基准值; Ps=3.304 MPa。
球阀一次薄膜应力整体强度的判断:
式中: Am 为金属界线面积, Am=750.77mm2; Af 为流体界 线面积, Af =1 566.60 mm2。\
计算可得, Pm=8.55 MPa<[σ]=123.4 MPa (260 ℃下, 316Ti 的许用应力), 所以一般状态下能够符合设计标准。
1.3.2 校核一次薄膜应力加弯曲应力
应用标准在 A 级的情况下, 球阀进行校核一次薄膜 应力加弯曲应力公式为: Pm + Peb < 1.5S
Pm 为一次薄膜应力, Pm = 8.55 MPa; Peb 为弯曲应力, Peb =

; Cb = 0. 115, 由于 Cb ≤ 1, 取 Cb = 1;

0.393d3 P
Gb 为危险截面弯曲的断面模数:
Gb =

(6)
S 为 260 ℃状态下管道材料屈服强度, 材料未知, 取 S =200 MPa; 又 Gb = 42 573.98; Peb = 5.3 MPa; 故 Pm + Peb = 13.85 < 1.5 [ σ ] = 5.3 MPa, 满足要求。
2 球阀阀口强度的有限元仿真分析
在构成阀口的构件中, 阀体是最关键的环节, 承担 着流动渠道和承受压力的重要功能[11]。分析阀体的作业 环节, 工作流体一直冲击内壁, 在阀口工作过程中, 阀 体的内壁受到工作流体冲击, 垫片力和螺栓力都由不同 的法兰分别承受, 同时在关闭阀门后, 阀座又要遭受密 封力的冲击[12]。另外, 阀体更要应对工作介质的水温波 动、水击、振动等形成的附加力, 除了各种力的施压, 还要面临工作介质的冲击和腐蚀。
基于球阀表现比较复杂的工况, 针对阀体应力的布 置必须重视解决两个问题: (1) 应力集中问题; ( 2) 最 大应力位置。应力集中与球阀的结构有关, 局部区域形 成的高应力是最大的威胁, 也影响承载能力的提升。可 能出现应力相对集中区域包括阀体与板筋及法兰相连的 位置、阀座底部倒圆角以及厚壁变化的地方等。最大应 力位置是阀体设计的重点, 在初步确定设计方案后, 需 要通过强度校核结果来客观判断阀体是否能够运行。若 最大应力位置承受的实际应力超出材料本身的强度极限, 则装置的运行势必会受到影响。设计过程中, 载荷分布 差异以及球阀的构造等因素, 都可对应力分布情况产生 影响。
2.1 有限元仿真分析步骤
对于本文介绍的仿真有限元分析法, 第一个步骤就 是建立模型, 其目的就是构建一个可以表现实际原型设 计的数学模型。建模的步骤也是整体系统的预处理过程, 为后续的数据运算提供全面的初始数据, 比如单元、节点和界线条件等。因为模型的构建方式可以左右数值运 算的精度, 而且整个仿真分析时间 72% 都花费在模型建 立上, 所以, 建模的质量和效率是整体有限元仿真分析 质量优劣的关键因素。本文研究的第一步就是建立阀体的实体模型, 以此 为依据构建仿真分析模型, 可以通过以下步骤进行。
( 1) 三维模型构建。基于 ANSYS 的三维建模有构建 实体模型以及直接生成两种策略。后者需要操作者手动 入手各个节点的坐标, 需要提前对拟建模型的单元规格、 各部分之间的内在联系等要素进行综合考虑, 提前完成 各种相关计算, 且直接生成的模型具有高差错风险、难以调整等特点, 在仿真分析中并 不常用, 一般只用于简单模型的 构建。本研究针对球阀设计, 球 阀模型属于复杂模型, 考虑使用 构建实体模型法, 按照组建几何 模型→ 划分网格→ 生成有限元模 型的次序有序构建三维模型。出 于算法层面的考虑, 本球阀的几 何模型使用 Solidworks 完成构建, 具体如图 3~4 所示。需要说明的 是, 阀口的建模难度偏高, 计算 量、占用内存空间较大, 且阀口 仿真不是此次研究的重点, 故本 模型对其进行了适当简化。
图 3 球阀整体三维图
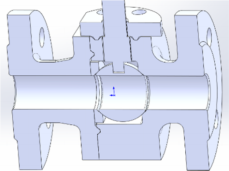
图 4 阀体剖面图
将三维模型导入 Solidworks 中, 以 sat 格式保存文件, 在有限元仿真软件中将文件输入。
( 2) 设定有限元仿真条件。分析类型为 structural, 单元为 solid187; 各项同性材料等同于阀体, 杨氏模量 E = 2. 1 × 105 MPa, 泊 松 比 μ = 0.26, 同 时 根 据 重 力 影 响, 给出密度ρ = 7.85 g/cm3, 重力加速度 9.8 m/s2; 智能 网格可以设定最精细的一级, 控制整体的单元规格为 5 mm; 固定两端面的同时进行 Y 向剖面固定; 进行载荷和 约束的施加; 进行全约束法兰断面, 以 Y 向约束剖面。
将适宜的压力和载荷施加到流体与阀口接触面; 本次采 用 PCG 预条件共扼梯度法作为阀口的有限元仿真分析 求解器。
( 3) 结果分析。在笛卡尔坐标系中检查模型中各个 节点的具体情况, 参考模拟结构, 确定测试坐标, 并根 据应力值、应变和云图的变形情况, 进行阀口承载状况 的分析。
( 4) 材料属性的确定。可以设定运算系统中阀口应 用的材料等同于各项同性材料, 在进行阀口应力分析过 程中不仅要确定泊松比, 更要考虑阀口材料的弹性模量、 密度等因素。
( 5) 划分智能网格。划分网格单元的原则为“粗划 分适用均匀的应力区, 细化分适宜应力梯度大的区域”, 对球阀的网格划分结果如图 5 所示。
图 5 模型的网格划分结果
( 6) 施加约束和载荷。 ANSYS 软件允许在有限元或 者实体模型上施加载荷, 而载荷方式的选择不会对作用 结果产生影响, 初始化完成后, 载荷作用可以顺利地转 换至模型上。与在有限元模型上施加约束、载荷的方式 相比, 直接作用于实体模型不受网格限制, 且操作简单, 因此, 本研究考虑直接作用于实体模型的策略, 将全约 束施加至法兰断面, Y 向约束施加到剖面上。将压力载 荷施加到流体和阀口内的接触面上。必须考虑重力原因, 将Z向重力加速度设定为 9.8 m/s2。
( 7) 求解计算。本研究采用 PCG 预条件共扼梯度法 作为求解器, 因为该方式最符合精细网格模型和实体模 型的求解, 在有限元软件家族中占据重要地位。
综上所述, 本研究的有限元仿真设定以下条件: 结 构静力学模型, 单元为 solid187; 阀体材料的杨氏模量 E = 2. 1 × 105 MPa, 泊松比μ = 0.26, 密度ρ = 7.85 g/cm3, 重力加速度 9.8 m/s2; 设定的智能网格为一级, 总体的单 元规格限定在 5 mm; 通过三相固定两端面, 以 Y 向固定 剖面; 求解器采用共扼梯度法 PCG。
2.2 有限元仿真结果分析
球 阀 阀 体 壁 厚 9 mm, 阀 体 材 料 为 WCB, 全 称 为“可焊高温用碳素钢铸钢”, 根据 ASTMA216 标准, 其 抗 拉 强 度 σ b = 485~655 MPa、 屈 服 强 度 σ s = 250 MPa, 杨 氏 模 量 E = 2. 1 × 105 MPa, 泊 松 比 μ = 0.26, 密 度 ρ = 7.85 g/cm3。球体材料 A105+ENP 用 ENP 工艺处理的 锻 钢, 其 抗 拉 强 度 σ b ≥ 540 MPa、 屈 服 强 度 σ s ≥ 315 MPa, 杨 氏 模 量 为 E = 2. 1 × 105 MPa, 泊 松 比 μ = 0.26, 密度ρ = 7.85 g/cm3。
材料的许可破坏应力除以安全系数, 就可以求解出材料的许用应力, 我国的相关标准中规定抗拉强度安全 系数的最小值为 3, 而屈服强度的最小值为 1.6。因此, 针对许用应力, WCB 材料为[ σ ] = 156 MPa, 球体材料 A105+ENP 为[ σ ] = 196 MPa。设定球阀在 Z 向重为加速 度为 9.8 m/s2, 压力载荷为 P = 2 MPa 时的应力云图。
( 1) 球阀的等效应力分布
第三强度理论认为, 在材料承受的应力强度超过其 许用应力之后, 材料将出现屈服破坏现象。而根据第四 强度理论, 排除温度变化带来的影响, 在静载条件下, 弹性体的受力达到一定条件出现明显变形后, 可出现材 料破坏现象, 而畸变能密度在这一过程中有着关键作用。 等效应力类似于上述的畸变能密度, 材料破坏表现如下 的强度条件:

] ≤ [ σ ] ( 8)
式中: σ 1 , σ 2 , σ 3 分别为 3种主应力; [ σ ] 为材料的许用应力。
如图 6 所示, 球体的最大应力区为内壁中部和底部, 应力最大值为26.29 MPa, 明显低于WCB材料的许用应力。
图 6 球阀的等效应力云图
( 2) 球阀的环向应力分布
图 7 所示为球阀的环向应力云图, 由图可知, 有较大应力在球体内壁中, 最大应力为 8.60 MPa, 许用应力 明显低于 WCB 材料。
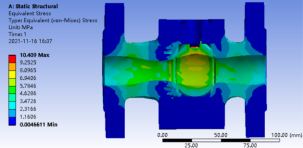
图 7 球阀的环向应力云图
特种球阀的结构设计是电厂球阀设计的难点, 既往 的公式估算方法以及经验系数在面对特种球阀设计任务 时容易出现失效现象。本研究从现有电厂球阀的结构设计经验出发, 对设计过程中的球径、阀体最小壁厚参数 计算进行了说明, 并对球阀强度性能的方针分析做了讨 论, 提出了一种能够有效应用于球阀强度校验的仿真分 析方法。从校验原理与分析结果来看, 本研究提出的有 限元仿真分析方法能有效处理特种球阀的强度校验问题, 根据球阀设计的实际要求, 合理确定有限元仿真分析的 条件,软件输出的等效应力云图、环向应力云图将帮助设 计人员准确地判断球阀的设计强度, 规避球阀设计缺陷。
3 结束语
通过分析目前对电梯制动性能无载荷检测技术的分 析比较, 目前, 通过空载试验有效评价电梯有载下行制 动性能的方法和测试设备很少。另外, 现有的检测技术 只提供了检测结果, 未提供整个制动过程分析, 明确导 致制动性能下降的具体因素, 例如控制系统响应时间、 制动器动作响应时间等更详细的内容, 以便能够根据这 些数据, 为电梯制动性能的调整提出方案和整改方向。 在提高现场检验的准确度、便捷度的同时, 还提升了检 验的服务质量、服务水平。
随着检验方法的不断创新发展, 新的检验技术也将不断更迭,会有更好的检测方案和电梯发展技术和要求相适应, 保证电梯的安全运行。
参考文献:
[1] TSG T7001-2009,电梯监督检验和定期检验规则— 曳引与强 制驱动电梯(含第 1 、2 号修改单)[S].
[2] 陈建勋 . 电梯制动性能无载荷检测技术研究进展[J]. 西部特种 设备,2020(10):40-45
[3] 赵晓涛 . 对永磁同步曳引驱动电梯制动试验的分析[J]. 机电工程技术,2020,49(5):51-52.
[4] 朱振国, 陈寅生,万莅新,等 . 一种曳引驱动电梯 125% 额定载荷制动试验无载测试装置[J]. 中国电梯,2021,32(19):45-47. [5] GB/ T 24478-2009,电梯曳引机[S].
[6] 沈永强 . 无补偿链(绳)电梯制动性能无载测试方法[J]. 特种设 备安全,2018(6):40-42.
[7] 焦一帆 . 曳引式电梯定期检验载荷试验的必要性探讨 [J]. 机 电工程技术,2020,49(3):99- 102.
[8] 许林,孙惟宁,刘畅,等 . 一种曳引电梯 1.25 倍制动试验无载测 试装置及测试方法[P].2019-01- 16.
[9] 周叶平, 秦智军, 汪有韬,等 . 电梯制动器安全性能监测方法综 述[J]. 机电工程技术,2020,49(12):123- 125.
[10] 宋云鹏,刘铁 . 电梯制动性能无载测试方法[P].2009-4-30.
[11] 刘天 . 电梯制动性能检测方法研究[J]. 中国新技术新产品 , 2018,12(上):58-59.
[12] 柳阳 . 基于本质安全的电梯制动器检验与分析[J]. 中国电梯, 2020,31(10):40-42.
关注SCI论文创作发表,寻求SCI论文修改润色、SCI论文代发表等服务支撑,请锁定SCI论文网! 文章出自SCI论文网转载请注明出处:https://www.lunwensci.com/ligonglunwen/45068.html