SCI论文(www.lunwensci.com):
摘要:在数控粗车加工工艺过程中,由于待加工零件表面不均衡,车刀切削深度波动大,导致数控机床主轴负载扰动较大,并且加工切削参数通常固定,不能实时修调,存在车刀磨损严重、不利于延长刀具寿命的问题。因此设计了一种基于模糊控制算法的恒功率车削智能控制系统,以保持主轴功率恒定为约束条件,使用WB6830R2-P采集功率数据,西门子PLCS7-200SMART开发主轴功率数据分析系统,WinCC 7.4用于开发上位机监控系统,利用二维模糊控制器计算合适的进给倍率,通过调整坐标轴进给速度使主轴功率保持在目标值附近。以汽车变速箱的核心零部件DCT150换挡毂车削工艺为加工对象,在ETC3650数控车床上设计车削实验,功率误差不超过40 W,实验结果表明,设计的恒功率智能控制系统对数控车床控制效果好,系统响应速度较高。
关键词:换挡毂;恒功率;模糊控制
Research on Constant Power Control System for CNC Turning of DCT150 Shift Hub Based on Fuzzy Control Algorithm
Dai Yuming,Xu Jinyu※,Guo Aolun,Peng Yujia,Wen Cong
(Hubei Institute of Automotive Industry,Shiyan,Hubei 442002,China)
Abstract:In the process of CNC rough turning,due to the uneven surface of the parts to be processed and the large fluctuation of the cutting depth of the turning tool,the load disturbance of the spindle of the CNC machine tool is large.The machining cutting parameters are usually fixed and cannot be adjusted in real time.The turning tool is serious wear,it´s not conducive to extending tool life.So an intelligent control system for constant power turning based on fuzzy control algorithm was designed.Keeping the spindle power constant was taken as a constraint,WB6830R2-P was used to collect power data,Siemens PLCS7-200SMART was used to develop the spindle power data analysis system,WinCC7.4 was used to develop the upper computer monitoring system,and the two-dimensional fuzzy controller was used to calculate the appropriate process,keeping the spindle power near the target value by adjusting the feed speed of the coordinate axis.Taking the turning process of DCT150 shift hub,the core component of automobile gearbox as the processing object,the turning experiment was designed on ETC3650 CNC lathe,and the power error was not exceed 40 W.The experimental results show that the constant power intelligent control system has a good control effect on the CNC lathe,and the system response speed is high.
Key words:shifting the hub;constant power;fuzzy control
0引言
加工过程模糊控制是机床智能化的重要体现,也是体现产品质量重要保证,现阶段加工高精度工件主要有3种方案值得广泛关注。徐剑[1]基于SINUMERIK 840D数控系统着重分析了几何误差自适应控制、自适应优化控制和自适应约束控制。其中几何误差自适应控制通常以被加工工件的尺寸精度或表面粗糙度为指标,通过检测机床的温度误差、几何误差等实时调整机床的加工参数,以保障加工精度,但实现难度较大。刘权[2]和刘恒丽[3]针对铣削工艺,以切削力为研究对象,提出基于数控系统自带功能开发的自适应控制切削技术方法。上述研究多以铣削工艺为研究对象,基于数控机床内置传感器实现自适应控制,系统开发成本较高,可移植性较差,不利于推广应用。
本文以汽车变速箱的核心零部件DCT150换挡毂车削工艺为加工对象,其单面加工包含车削特征、铣削特征、102项尺寸,如图1所示,该结构特点属于精密薄壁腔体类零件,加工要求严格[4-8]。因此,本文在数控车床ETC3650上设计实验,开发基于二维模糊控制算法的恒功率智能车削控制系统,实现进给速度自适应调整,提高加工过程的稳定性[9-12]。该设计方案在老旧机床或多厂商数控机床适应性强,具有开发成本低的优势。
1模糊控制决策设计
根据专家经验和数据总结建立规则库,模糊推理和逆模糊化。其模糊控制结构如图2所示。在设计中,首先设定目标切削功率P,将目标切削功率P与切削加工中实际测量得到的主轴切削功率Po进行比较,以获得误差Ep和误差变化率EU。设E和EU相对应的模糊变量为SE和SEC。将其输入模糊控制器进行模糊化处理,处理后获得进给倍率调整量Δu再输入PLC,最终改变机床主轴进给速度,实现切削过程的智能控制。该过程采用循环控制方法,实现切削过程的主轴功率有效保持在目标切削功率P附近。
1.1模糊化
进行模糊化时首要做的是将功率分为7个区间{<440,440~470,470~500,500~520,520~550,550~580,>580}。实际功率值跟该7个区间比较,通过组合大、中、小和正、负两个方向概念,另外再加入变量为零的状态,一共可以形成7个词汇,即{负大,负中,负小,零,正小,正中,正大},对应的模糊子集为{NB,NM,NS,ZE,PS,PM,PB}。每一个功率值可以进入相应的功率区间,从而改变进给倍率。初始给定的进给倍率为100%,模糊控制在此基础上进行修调。设误差率EU的基本论域为[-0.06,0.06],变量EU、Ep的量化模糊论域依次为{-15,-7,-1,0,1,7,15},Δu论域依次为{-15,-8,-2,0,2,8,15}。
1.2模糊规则和决策设计
采用Mamdani控制规则进行模糊推理运算,根据工艺工程师和电气工程师长期对车削加工的实践经验总结,可设置模糊规则如表1所示。
由上述模糊控制规则和图3所示的三角形隶属度函数,构建模糊推理控制系统。
2设计原理
基于ETC3650数控车床和GSK988T型广州数控系统,以西门子S7-200SMART为下位机,使用OPC通信连接WinCC,使用功率传感器采集功率,设计一种换挡毂车削加工恒功率自适应控制系统,使得在加工过程中各种扰动量作用下,控制系统能够自动调节车削进给量以达到恒功率切削的目的。用功率传感器将主轴的功率采集出来,并送入PLC中分析计算,在PLC中进行模相控制,通过改变进给倍率来控制主轴恒功率,当功率偏大时,减小进给倍率,当功率偏小时,增大进给倍率。并将采集到的功率曲线在WinCC中显示出来,实时监控车削加工功率。图4所示为整个系统的设计框图。
3硬件设计
该系统硬件为:WB6830R2-P三相功率传感器、I/O单元扩展模块CB106、24 V开关电源。通过三相电和24 V直流电的供电,以及功率传感器的数据采集,完成基于STEP-7的模糊控制,I/O单元的数据输入,对车床车削过程恒功率自适应控制。利用S7-200 SMART SR/ST CPU模块本体集成1个以太网接口和1个RS485接口,通过扩展CM01信号板或者EM AM06模块,其通信端口数量最多可增至4个,可满足小型自动化设备与触摸屏、变频器及其他第三方设备进行通信的需求。
通过功率传感器的模拟量输出至S7-200SMART扩展模块OUT1,通过WinCC7.4开发监控系统并进行数据分析比较,结果信号输入I/O单元,实现数控系统对伺服驱动器控制的主轴倍率控制。
三相功率传感器采集模块电气原理如图5所示。PLC及AD模块电气原理如图6所示。
4软件设计
根据模糊控制器设计方案,模糊控制算法主程序设计流程如图7所示。首先通过监控界面(图8)设置目标功率值,控制系统通过功率采集模块实时获取功率,如果功率值在标定范围内,则计算功率误差和误差变化率,并进行模糊化,再通过模糊推理和非模糊化计算出主轴进给倍率调整值。进给倍率调整值与当前进给倍率值求和获得进给倍率值。最后通过I/O模块传入PMC,最终以达到改变车床主轴进给速度的目的。
主轴功率数据采集G代码如下:
G28 U0 W0
T0101
S2000 M03
G00 X40 Z5
G00 X17
M74
G99 G01 Z-60 F0.3
M75
G00 X40 Z5
M05
G28 U0 W0
M30
将铝棒作为预实验工件,预先将其切削成3种不同直径的阶梯状圆柱,直径依次为小20、小19、小18。
编制外圆车削为阶梯状的G代码程序:
G28 U0 W0(设定刀头原点)
T0101(1号刀及刀补)
S2000 M03(转速、主轴正转)
G00 X40 Z5(刀头起始点)
G90 X20 Z-60 F0.3
G90 X19 Z-40
G90 X18 Z-20
M05(主轴停转)
G28 U0 W0(回刀头原点)
M30
5验证与结果分析
本文开发的数控车削恒功率控制系统在ETC3650数控车床上进行实验验证。如图9所示,刀具选用直径为20 mm的超硬PCD车刀。设计两个实验进行验证:实验1用阶梯状铝棒为加工零件,进行外圆车削恒功率控制实验验证,该实验作为预验证,并进行对比实验;实验2用汽车变速箱的核心零部件DCT150换挡毂为加工零件,进行车基准面加工实验验证,该实验作为应用验证。两个实验的加工零件材料保持一致。
图9 ETC3650数控车床
(1)阶梯状铝棒预对比实验
加工图10所示的阶梯状铝棒零件,刀具沿着铝棒轴向进给车削,加工参数为:主轴转速2 000 r/min,被吃刀量2.5 mm。

图10阶梯状铝棒零件
传统加工模式与智能控制模式功率对比如图11所示,图中A曲线是没有加入功率自适应控制的功率曲线,有明显的阶梯状,B曲线是加入恒功率控制之后的功率曲线,由图可知在加入恒功率控制后,系统在运行稳定时,功率曲线变得平滑,没有阶梯状的曲线出现;这样做可以有效地保护刀具减少其损耗,提高加工效率,减少加工时间及能源消耗。
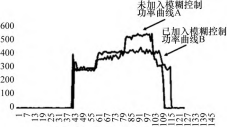
图11传统加工模式与智能控制模式功率对比曲线
(2)DCT150换挡毂应用实验
加工参数为:主轴转速3 000 r/min,被吃刀量1.5 mm。对比结果如图12所示,由图可知,DCT150换挡毂应用实验加入模糊控制后车削功率基本维持在目标功率620 W附近。
(a)未加入模糊控制(b)已加入模糊控制
图12加入模糊控制前后车削功率
6结束语
本文以ETC3650数控车床作为加工平台,设计了基于模糊控制智能控制系统。采用二维模糊控制算法调整进给倍率,实现车床主轴恒功率切削控制。通过阶梯状铝棒预对比实验,对恒功率控制系统实现预验证。然后通过在汽车变速箱的核心零部件DCT150换挡毂基准面车削工艺开展应用实验,实验表明在使用自适应控制系统后,进给倍率随主轴负载不断调整,实时功率基本保持在目标功率附近,提高了车削效率,并且减少刀具损耗,对延长刀具寿命有一定的参考价值。
参考文献:
[1]徐剑.基于SINUMERIK840D数控系统的恒功率自适应控制方法研究[D].南京:南京航空航天大学,2015.
[2]刘权,滕永鹏,余昌水,等.基于主轴恒功率的铣削过程工艺参数自适应调整方法研究[J].工具技术,2021,55(5):67-70.
[3]刘恒丽,王勇,董靖川.基于动态特性的数控铣削参数自适应在线优化[J].制造业自动化,2019,41(9):82-88.
[4]王泽学.我国车企DCT双离合变速器开发现状分析[J].时代农机,2016,43(5):71.
[5]高成浩.乘用车双离合变速器加工工艺设计的探析[J].汽车工艺与材料,2015(8):26-29.
[6]韦昊,李志远,于博,等.双离合变速器技术原理及发展前景[J].科技创新导报,2017,14(9):74-75.
[7]王金钢,张金虎,徐哲,等.双离合变速器换挡毂关键工艺技术研究[J].轻工科技,2018,34(12):42-43.
[8]马振新.双离合变速器简介[J].农机使用与维修,2012(2).
[9]王文理,袁士平.自适应加工技术在数控加工领域的分类与应用[J].航空制造技术,2013(6):26-29.
[10]Huang M G.The restraining of machine vibration based on the optimized servo control[J].Applied Mechanics and Material 2012(184-185):1592-1594.
[11]Zuperl U,Cus F,Milfelner M.Fuzzy Control Strategy for an Adaptive Force Control in End-milling[J].Journal of Materials Processing Technology,2005(164/165):1472-1478.
[12]Xu G D,Chen J H,Zhou H C,et al.Multi-objective Fee-drate Optimization Method of End Milling Using the Internal Data of the CNC System[J].The International Journal of Advanced Man⁃ufacturing Technology,2019,101(1/2/3/4):715-731.
关注SCI论文创作发表,寻求SCI论文修改润色、SCI论文代发表等服务支撑,请锁定SCI论文网!
文章出自SCI论文网转载请注明出处:https://www.lunwensci.com/ligonglunwen/49801.html