SCI论文(www.lunwensci.com):
摘 要:供应商管理是制造业企业的重要影响因素之一, 随着产业链、供应链的发展,越来越多的企业开始重视 供应商管理。本文以T企业为例,为制造业企业提供了判 断重要供应商的方法,建立了供应商重要性模型。具体 来讲,就是定义了反映供应商供货能力的6个指标,求出 KMO值并进行Bartlett检验,然后通过因子分析得出402家 供应商可靠性得分和排名,从而帮助T企业根据排名选取 重要的供应商。本研究旨在帮助企业判断和选择合适且重 要的供应商,提升企业供应商管理水平。
关键词:供应商重要性模型;因子分析;选择供应商
一、前言
供应商在企业的生产环节中起着重要的作用, 它 为企业提供各种所需资源,包括原材料、设备、能 源、劳务和资金等,优良的供源和交付能够提高最终 产品和服务的质量,从而提高其市场竞争力。同时, 由于原材料在从供应商到生产企业之间需要经过转运 商转运和仓储,因此在转运过程中的原材料损失、转 运费以及仓储费都占用企业生产一部分支出。
现有T企业生产需要A 、B和C三种原料,该企业每 年按48周安排生产,需要提前制定24周的原材料订购 计划,为了保证生产需要, T企业要尽可能保持不少于 满足两周生产需求的原材料库存,为此T企业对供应商 实际提供的原材料全部收购。此前T企业已经对402家 供应商进行过订货,现在对402家供应商的供货特征进 行量化分析,建立反映保障企业生产重要性的数学模 型,并在此基础上确定50家最重要的供应商。
二、文献综述
查阅文献得出, 企业为降低在原材料方面的总成 本一般从三个方面入手,分别是选取最佳供应商,制 定最优原材料预定方案以及制定最优转运策略。
选取最佳供应商。对能够满足企业要求供应商, 通过计算其综合成本,选择能够持续供货以及成本较 低的供应商。Timmerman等[1]提出成本比率法,通过计 算出跟成本有关的项目的成本占总成本的百分比来确 定要选择的供应商;Filip Roodhooft等[2]提出活动成本 法,在选择最优供应商时,需同时考虑由采购活动产 生的直接成本和间接成本。
制定最优原材料预定方案。对满足企业生产需要 的原材料,通过计算比较采购成本并根据上述已经确 定的最佳供应商综合考虑选择出最优原材料订购方 案。 Koji Muteki等[3]提出了以最低成本实现所需产品质 量的原材料的最佳采购方法。
制定最优转运策略。为了确定最低转运成本, 通 过计算转运和仓储成本以及转运商转运损耗率,得到 最优转运策略。 Chao Liang等[4]考虑到转运成本和需求 分配形状的影响,研究了公司的最佳转运问题。
目前国内外学者对此类问题已经有所研究, 吴隽 等选择模糊质量功能展开的方法(QFD)进行供应商 的选择[5];Chan等为了讨论全球采购相关的问题,选择 了模糊的层次分析法(fuzzy-AHP) [6];Boran等采用的 直觉模糊TOPSIS方法解决该问题[7]。
本文基于已有学者研究, 定义了决定供应商供应 能力的6项指标——供应商供货总周数、负责程度、竞 争能力等,之后基于数据求出 KMO 值并进行 Bartlett 检 验。数据通过检验后,进行因子分析得出所有供应商可 靠性得分,最后将得分排名确定了供应商的重要性。
三、指标统计分析
供应商的供货能力受到多方面因素影响, 为了尽 可能对其供货能力进行综合全面描述,为对供应商的 供货特征进行量化分析,选取了如下指标,依次对其 进行分析评价。
指标一: 企业对供应商的需求程度。供应商近一 年内对企业供货总周数(x1 ),其中企业的供货总周数为( wg )。
x1 = wg (1)
指标二:供应商满足企业货物需求能力。由于有 时企业向供应商提出需求后,供应商不能提供企业足 够数量货物,因此定义供应商满足企业货物需求能力 (x2 ),为供应商供货总数与订货总数比值(其中gi为 第i周供应商供货数量, di为第i周企业订货总数)。

(2)
指标三:供应商按照企业订货数量提供货物的负 责任程度。为了反映供应商按照企业订货数量提供货 物的负责任程度(x3 ),排除供货量大于订货量该企 业生产保障能力强的情况,只挑取订货量大于供货量 的数据,令订货周数中每周订货数量(di )与供货数量 (gi )之差后平方之和与供应商供货总量(wd )之比作 为指标三。
x3 =

(di > gi ) (3)
指标四:供应商之间的竞争能力。为了反映相同 货物供应商之间的竞争能力(x4 ),我们采取了将每 周各种货物订购数量与该货物的企业数量之比作为该 种货物类型企业平均责任供货数量,并统计各个企业 大于该平均责任供货数量周数(s)作为该指标。
x4 = s (4)
指标五:供应商相对供货能力。为了描述供应商 的相对供货能力(x5 ),将供货总数与订货周数(wt ) 之比作为指标五。

(5)
指标六:企业对供应商的依赖程度。为了反映企 业对供应商的依赖程度,将企业向供应商的供货数目(gi )求和作为指标六(x6 )。
x6 =

gi (6)
四、基于因子分析的供应商选取模型
(一)模型的建立
依据上述6项指标x1, x2, x3, ..., x6 ,基于402家供 应商, 其样本观测值为xik ( i=1, 2, ..., 402; k=1, 2, ..., 6)。以 xk 为xk的平均数, sk为xk标准差,经过 标准化变换, xk变为,得到
x*k =

(7)
(二)模型的分析
计算因子得分,并进行综合评价用回归方法计算 各个因子得分函数:
F%j = βj 11+ βj 2 2 + L + βj 6 6 (8)
则有
Fˆ = ( )402×2 = X0R − 1A2 (9)
其中 X0 = (ij)402×6为原始供应商数据的标准化数据矩阵; R 为相关系数矩阵; A2 是上述过程中得到的载荷 矩阵。
(三)模型的求解
1.分析KMO值和Bartlett 检验
对数据进行分析KMO值和Bartlett 检验,得出结果 见表1所示。
表1 KMO值和 Bartlett的检验

KMO值为0.688,大于0.6,通过Bartlett 球形度检 验(p < 0.05) 满足因子分析的前提要求,即数据可用于 因子分析研究。
2.主因子选取
得出初等载荷矩阵,见表2所示。
表2 初等载荷矩阵

基于上述分析,本文选取了3个主因子,随后利用 SAS软件计算得到旋转后的因子贡献以及因子贡献率, 见表3所示。
表3 贡献率数据

最大方差正交旋转后,得到了6个指标在3个因子 上的新因子载荷。
得出各个因子的得分函数为:综合因子得分公式:
将各项数据代入公式(10),求得所有供应商综 合供货能力得分及排名。为使结果更加直观,将前 五十组供应商得分绘制柱状图,见图1所示。
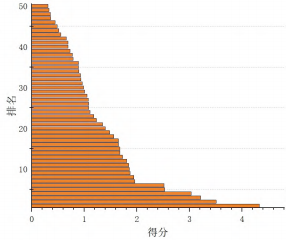
图1 前50组供应商得分分布情况
综上,为了保障企业生产重要性,企业在选择供 应商时,应当综合考虑供应商供货能力。
五、结论
本文是将供应商的供货特征进行量化分析,建立 反映保障企业生产重要性的数学模型,以此来选择最 重要的供应商,同时结合转运过程中的各种损耗情 况,以此来确定所需的供应商最少数目。本研究选用 T企业近5年402家原材料供应商的订货量和供货量数据以及8家转运商的运输损耗率数据进行分析,得出相 关结论。企业在选取重要供应商时应选择需求程度较 高、满足企业货物需求能力较强、按照企业订货数量 提供货物的且负责程度较高、竞争能力较强、供货能 力较强的供应商。
参考文献
[1] Timmerman E An Approach to Vendor PerformanceEvaluation[J].IEEE EngineeringManagement Review, 2007, 15(3):14-20.
[2] Roodhoofl F,Konings J.Vendor selection and evaluationall Activity Based Costing approach[J].European Journal of Operational Research, 1997, 96 ( 1 ):97-102.
[3] Muteki, K.and MacGregor, J.F.Optimal purchasing of rawmaterials:A data-driven approach[J].AIChE J, 2008 ( 54 ):1554-1559.
[4] Liang, C., Sethi, S.P., Shi, R.and Zhang, J.InventorySharing with Transshipment:Impacts of Demand Distribution Shapes and Setup Costs[J].Prod Oper Manag, 2014 ( 23 ):1779-1794.
[5] 吴隽,王兰义,李一军.基于模糊质量功能展开的物流服务供应商选择研究[J]. 中国软科学, 2010 ( 3 ):7.
[6] Chan F T S, Kumar N, Tiwari M K, et al.Global supplierselection:a fuzzy-AHP approach[J].International Journal of Production Research, 2008, 46 ( 14 ):3825-3857.
[7] Boran F E, Gen? S, Kurt M, et al .A multi-criteriaintuitionistic fuzzy group decision making for supplier selection with TOPSIS method[J] . Expert Systems withApplications, 2009, 36 ( 8 ):11363-11368.
关注SCI论文创作发表,寻求SCI论文修改润色、SCI论文代发表等服务支撑,请锁定SCI论文网!
文章出自SCI论文网转载请注明出处:https://www.lunwensci.com/guanlilunwen/49392.html